The manufacturing industry is positioned for growth due to several factors, including reshoring efforts and the expansion of sectors such as defense, medical, and space. This demand for growth is driving the adoption of new technologies that enable manufacturers to stay competitive, including automation, additive manufacturing, generative artificial intelligence (Gen AI), and digital twins and simulations. However, despite their potential benefits, barriers hindering their adoption remain.
Automation
Today, manufacturers face the new challenge of producing a wider variety of parts at lower volumes due to the rapid growth of multiple industries and a diverse portfolio. Luckily, automation remains a pivotal technology for manufacturers to achieve scale.
Current automation technologies are flexible for handling multiple parts and setups. Combining them with human-to-machine interfaces (HMI), which have been simplified to enable diverse programming methods, enables manufacturers to deploy and redeploy automation equipment. However, companies early in their automation journey are hampered by several issues, including not seeing a quick return on investment – often requiring more than one business cycle – and having an underdeveloped working knowledge of automation and safety protocols.
In an interview, Sami Birch, director of marketing at Mission Design and Automation, discussed some of the advanced technologies in automation fueling growth:
"We also anticipate the continued adoption of collaborative robotics in more spaces to augment high-mix, low-volume work as manufacturers of all sizes look for ways to improve quality and throughput while navigating ongoing labor challenges. Smart vision systems paired with robot integration systems will continue to improve, and we anticipate seeing them adopted further into more industries, beyond their e-commerce/warehousing mainstays, as traditional manufacturers seek ways to tend traditional automation amongst the labor shortage."
Additive Manufacturing
The ability to add complexity to a final product is key, which is where additive manufacturing shines. For example, a nozzle that can only be produced additively may enable different abilities or achieve higher tolerances than one produced traditionally. Such additively manufactured final products realize increased power, efficiency, and performance for the OEMs using them, providing a competitive edge. Space, defense, and medical applications are seeing these gains, which are in turn stimulating the growth of additive technologies and processes.
Even with these growth opportunities, barriers remain. Raw material costs are a challenge for additive manufacturers, but sustainability efforts in powder reduction and reclamation are driving increased adoption. Additionally, new material and process qualification standards have been a consistent barrier since the technology’s initial days. More recently, remote manufacturing has presented an opportunity for additive manufacturing, but the requirements for data management, rights, and life-cycle are unknown.
Gen AI
Generative AI (Gen AI) is here – likely forever. This technology has seeped into most aspects of everyday consumers. What makes this technology so ubiquitous and applicable to manufacturing? One aspect is the ease of use, particularly for summarization and data queries. Users using natural language can probe custom datasets to identify valuable opportunities, making adoption attractive to OEMs and job shops alike.
With this increased demand, the hardware to support AI mathematical models is evolving as well. There are more hardware and accessible solutions than ever before. This enables users to test, iterate, and produce AI-based solutions faster and reduce the cost of cloud-based solutions. Despite these benefits, implementation of Gen AI is still early; it will need beefier security and privacy protocols and increase the number off-the-shelf solutions for known manufacturing problems to really accelerate adoption.
Frank Nuqui, strategic program manager at Fanuc, outlines some of the challenges in integrating Gen AI:
"Manufacturers face concerns over data security, intellectual property rights, and significant upfront investments. Implementation can be disruptive, requiring workforce adaptation and careful navigation of ethical considerations. The potential for job displacement also warrants attention."
Digital Twin and Simulations
Digital twins are digital representations of a physical object. This requires metrology technologies to capture, process, and post-process 3D scans of the physical object. While digital twin technology by itself is not useful, when applied to simulations, end users can extract a competitive edge. Such benefits include predicting outputs, testing real-world conditions, and calculating results, thus enabling companies to improve everything in the manufacturing process, from design to maintenance schedules to workflow to end-use experience. This requires extensive modeling programming to set up and execute; luckily, the use of AI bolsters modeling and programming tools and accelerates the adoption of simulations.
Unfortunately, these advantages require a tremendous amount of technical expertise that is difficult to obtain. In addition to a company’s lack of expertise, the lack of industry standards further limits adoption. Currently, solutions are one-off productions or fall within the domain of proprietary solutions.
Conclusion
These emerging technologies are set to transform manufacturing processes, enabling greater efficiency, flexibility, and a competitive advantage. As manufacturers navigate manufacturing’s evolving landscape, collaboration between industry leaders, technology developers, and policymakers will be crucial to addressing the challenges currently hindering widespread adoption. Once these barriers are overcome, the industry will unlock new opportunities, drive sustainable growth, and remain at the forefront of global innovation. The future of manufacturing holds immense promise, and with strategic investments and a forward-thinking approach, the industry can thrive in the face of emerging trends and demands.
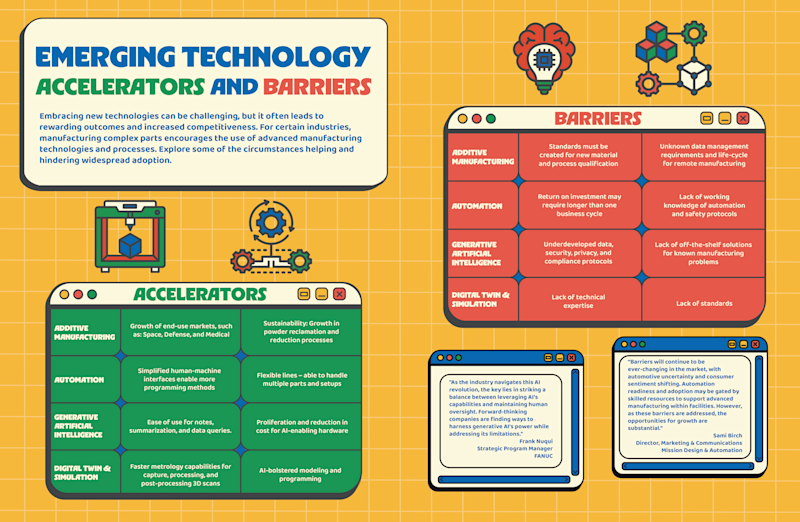
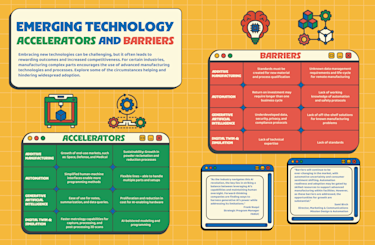