Despite the growing importance of the service sector, manufacturing is still the foundation of economic life in the United States. Almost everything that we use in our everyday life was touched by machine tools – appliances, transportation, medical and agricultural equipment, energy infrastructure, food and beverage production – the list goes on. Manufacturing is also a major engine of economic power, employment, and a source of innovation for the economy as a whole. Yet, it took the supply chain disruptions caused by the COVID-19 pandemic for some business leaders and politicians to understand how critical the manufacturing industry is to the United States and its national security – from securing medical supplies to providing basic components of everyday products.
Have the fundamentals changed?
CNCs created the industry we know today, and every decade has seen incremental improvements in production processes as we’ve learned more about the qualities and characteristics of the materials that we machine, new tools are developed, and 3-axis machines evolved to 5-axis machines.
“The fundamentals haven’t changed, but many improvements have made the industry more productive,” said Scott Smith, group leader, Intelligent Machine Tools at Oak Ridge National Laboratory (ORNL). “For example, we can now machine very thin monolithic parts, replacing sheet metal assemblies. We can machine very difficult materials while keeping both temperatures and tool wear to a minimum. And whereas NC programming was historically focused almost exclusively on the geometry of machined parts, it has now evolved to a point where we can quantitatively consider things like torque, power, stiffness, and surface finish while creating the part program.”
In the past decade, the productivity of CNCs has been increased through integration with new digital technologies – sensors, data collection and analysis, artificial intelligence, machine learning, edge computing – all of which have improved productivity, reduced waste, and freed workers from many menial tasks.
“The industry is moving from a model of one worker tending one machine to each worker tending many machines,” said Tony Schmitz, joint faculty, ORNL. “By leveraging what we can do with digital technologies, machines are operating more autonomously, and this trend will continue. Automation is imperative because one of the only ways the U.S. can remain competitive given wage differentials between countries is by increasing productivity.”
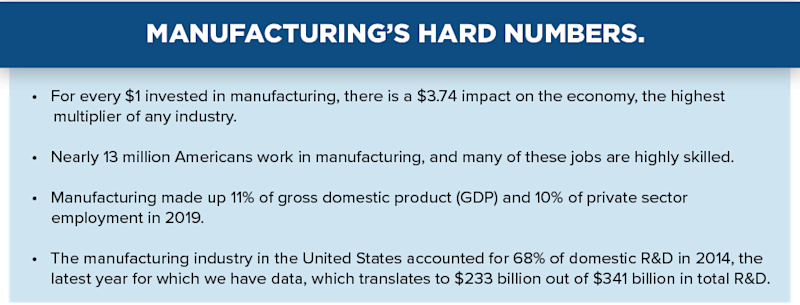
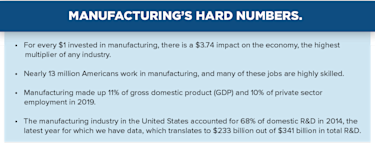
Cobots filling new niches
Another area of change is the introduction of cobots into manufacturing processes. “Cobots have found a niche and have emerged as the newest area of innovation and productivity,” said Stephen LaMarca, technology analyst, AMT. “Advances in sensors, AI, machine vision, and light detection and ranging (LiDAR), among other technologies, are making cobots easier to program, less expensive to deploy, and increasingly flexible in the types of tasks they can safely perform.”
Cobots are also ideal for smaller manufacturers, given their much-lower price point and how much easier they are to program and use, reducing or eliminating the need for engineering staff and lost productivity due to downtime.
Metrology
Another technology positioned to increase both productivity and quality is metrology, especially as it moves closer to the manufacturing process. “Many companies started by looking at data that represents the machine state but realized that what they really need to be looking at is finished parts to measure surface finish, microstructure, and geometry – qualities that indicate how the part is going to perform. As metrology continues to be integrated closer to the manufacturing process, we will get actionable data earlier in the process where better decisions can be made,” said Smith.
Training
Workforce training is one more part of the manufacturing ecosystem ripe for incremental improvements. Schmitz commented, “We need to change worker training to the realities of the new workforce. Many managers making training decisions today were trained in manual machining, but this may not be the best approach for millennials. They’re already comfortable in the digital domain, so it makes sense to start there and then move them into the physical realm. Their skill sets are different, and physical skills must be closely integrated with digital technology; this leads to creativity and innovation.”
Are changes adding up to industry disruption?
To ponder this question, we need to remember that industry disruption doesn’t happen overnight. That said, additive manufacturing (AM) may be an example of disruption or a model of how future disruption might happen. On the one hand, AM is being used to make highly regulated products in the aerospace and medical industries; on the other, the technology has been embraced by more than half a million people in the Maker Movement. We’ll break this down.
What does the maker movement represent?
Starting in the 2010s, the falling prices of 3D printers, coupled with free, open-source software on the web, brought a new generation of people, largely millennials, into manufacturing via AM. The low price point served to democratize and personalize the AM opportunities and creative space; anyone could play with it, experiment with it, and manufacture items. As industry analyst Jeremiah Owyang summarized, the Maker Movement put power in the hands of everyday people “to fund, design, prototype, produce, manufacture, distribute, market, and sell their own goods.” This sounds like potential disruption.
At the same time, technical colleges and engineering programs embraced AM and offered classes to students, and innovation hubs sprang up in regions such as the Bay Area and surrounding some of the big schools – Georgia Tech, Texas A&M, Carnegie Mellon, MIT, and many other locations. AM is still very much a part of the engineering curriculum at almost all technical and engineering schools. When students graduate, they take their skills and interests with them into the workforce.
A generation of disruption
We glimpsed the potential of AM as a market disruptor during the pandemic. While the U.S. supply chain was paralyzed and not able to obtain basic PPE, individuals and makers throughout the country stepped in and made both commercial and personal batches of PPE, delivering them to clinics, hospitals, and individuals.
Millennials are digital natives who grew up using and playing with digital technology. Because of their comfort with technology, they’ve been able to generate some of the most creative activity and thinking using it.
“To extend this concept, imagine if a type of CNC is developed that doesn’t require programming knowledge, has easy-to-use fixturing and tooling techniques, and functionality that makes CAD designs easy to develop, similar to what has happened with AM,” said Doug Woods, president of AMT. “This could become disruptive. We’ve seen disruptive technologies eliminate entire market sectors in the past decade, and while we don’t want to alarm the industry, it’s important that we think boldly about the future and what might happen so that we can be positioned for it.”