When the subject of the environment and sustainability comes up, some are all for it, while others, on their best behavior, roll their eyes and think, “I’ve got production schedules to meet; I don’t have time to do the things that people who don’t have the slightest idea about manufacturing think would be ‘good’ for me to do.” (Their less-than-best behavior would include an array of words that we can’t publish here.)
The latter approach is usually from people who see doing things “green” as yet another thing they have to do – when they are already busy enough without adding more tasks and activities to what they are trying to accomplish.
But implementing practices that minimize or eliminate (e.g., through different practices or via offsets) things like carbon in production materials and processes is becoming a requirement for suppliers at several companies that are working toward zero-emissions in their own production operations. From Audi to Whirlpool, an ever-increasing number of global manufacturers are making zero-carbon pledges. Whirlpool has stated that it is committed to achieving “Net Zero impact of our operations by 2030 and creating shared value throughout the product life cycle.”
And these companies aren’t just considering becoming carbon neutral within their own operations; this also includes suppliers. Audi has stated: “In 2025, on average, around 25 percent of total emissions that an Audi car will produce during its life cycle will be generated in the supply chain. To offset this, the company launched an ‘Audi CO2 program in the supply chain’ back in 2018. Together with suppliers, the program identified measures for CO2 reduction in the lower stages of the value chain.” Hard to imagine how they could emphasize suppliers more.
The point is, while global companies are making it clear that they are committed to carbon neutrality, they are also making it mandatory that suppliers support those efforts.
This Is Serious
Ford, for example, has published the Ford Supplier Code of Conduct that explicitly states requirements that every supplier must meet, including:
“Know and follow this Code and align company policies to reflect these requirements.”
“Enforce a corresponding code of practice and require that subcontractors and suppliers do the same.”
Which means that even second- and third-tier suppliers are included.
And the company is serious about this. It states in large letters and bold type that suppliers must:
“Comply with or exceed Ford’s environmental requirements and policies, including all relevant national, regional, environmental, and chemical legislation.”
“Minimize their impact on climate change aligned with the United Nations Framework Convention on Climate Change (Paris Climate Agreement), striving towards carbon neutrality.”
Reduce, reuse, recycle materials in manufacturing.
“Achieve continual environmental improvement in manufacturing operations.”
And there are details describing what is expected.
What’s Expected
Or take Boeing, which has more than 11,000 Tier 1 suppliers. In the company’s Supplier Code of Conduct, it states – and it is worth quoting at length because it underscores the importance the company places on the environment:
“We expect suppliers to conduct their business in a manner that actively manages environmental risks across their operations, products, and supply chain.
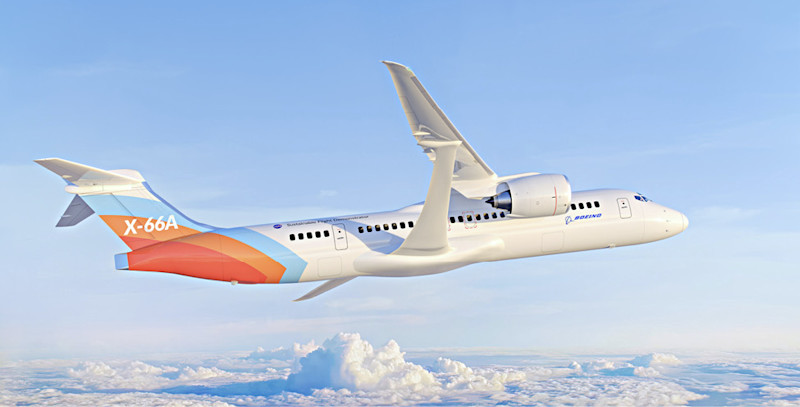
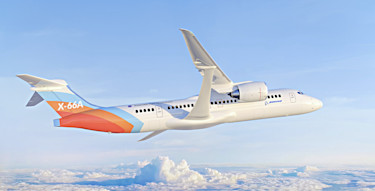
The X-66A research aircraft from NASA and Boeing is part of the Sustainable Flight Demonstrator Project. It will be built using a modified MD-90. Not only is Boeing working with NASA to help develop aircraft that allow airlines to cut aviation greenhouse gas emissions, but the company expects its suppliers to innovate to reduce the impact of their processes and products on the environment. (Image: Boeing)
“Suppliers are expected to establish an appropriate environment management system (e.g., ISO 14001 or equivalent), including policies and procedures aimed at effectively managing their environmental performance, and integrating environmental considerations into their product design or service.
“Boeing considers climate change to be an urgent issue and expects suppliers to innovate in order to reduce the impact of their products, services, and operations on climate change.
“We expect suppliers to improve the efficiency of their energy, water, and natural resource usage, to minimize hazardous waste materials, to dispatch goods in adequate outer packaging and foster reusable/recycled packaging materials, and to responsibly manage their air emissions.
“We expect suppliers to collaborate with Boeing to improve the processes and systems throughout the product lifecycle to protect the environment. Over time, we expect suppliers to establish environmental sustainability priorities and report their progress.”
Those that roll their eyes when it comes to their manufacturing and the environment are going to find themselves with eyes wide open with surprise if they don’t begin to transform their operations to keep up with the requirements of these major manufacturers. While a given company may not directly supply aerospace, appliances, or automotive (just to name three), their customers could be doing so, and all of these companies are looking up and down the supply chain.
Moving in the Right Direction
While there are some clear issues within a manufacturing operation that need to be addressed in order to move in the direction of a more environmentally appropriate approach – like the issue of chemicals used in processes (which may actually fall under regulatory rules, so this isn’t something that is not just nice to address but legally required) – there is something that can be done that will have benefits across the board.
Back in 1990, after the publication of “The Machine That Changed the World” by James Womack, Daniel T. Jones, and Daniel Roos, companies large and small started paying attention to lean production, which is defined by the Lean Enterprise Institute as:
“A business system for organizing and managing product development, operations, suppliers, and customer relations that requires less human effort, less space, less capital, less material, and less time to make products with fewer defects to precise customer desires, compared with the previous system of mass production.”
However, this isn’t an approach only valued by mass manufacturers. It benefits companies of all sizes.
Key Points
Fundamental to lean are the seven major wastes identified by Taiichi Ohno, the father of lean. Not only can eliminating waste cut costs and improve quality, they also have ramifications that can help achieve green(er) operations.
Overproduction.
This not only means excess product to the end customer but is also detrimental to the next step in the production operation. Making too many things is a waste of material and energy.
Waiting.
During production operations, if there is a bottleneck causing subsequent operations to wait, odds are the machinery in the shop is still running but not adding value to parts. The energy wasted can be significant.
Conveyance.
It is important to reduce the distance between operations within a facility, which saves both time and energy. Similarly, not only do supplier parks and reshoring help boost efficiency, but they reduce energy expended in transportation (which can result in emissions reduction).
Processing.
Understanding what the end customer is willing to pay for can result in products that meet those requirements. Analyzing the operations performed in the context of customer requirements (as well as engineering issues) may lead to the elimination of steps, which reduces material and energy requirements.
Inventory.
Ideally, no more inventory is on hand than is required to keep production flowing. Although the pandemic has changed what is considered necessary, excess inventories not only mean there are materials used and energy expended on components that may – or may not – be used, but the warehousing space can be a driver of waste (because it needs to be lighted and heated, for example).
Motion.
This is primarily an issue at the operator level. The operator does things that can result in physical strain or which are a waste of time, such as searching for tooling. Ergonomics and 5S principles (sort, set in order, shine, standardize, sustain) are simply good business practices that, when deployed, can minimize operational waste, like repetitive stress injuries to operators who subsequently need to be temporarily replaced (getting that person is important, but it doesn’t add value).
Correction.
Doing it again or scrapping it: clearly wastes of time, effort, and energy.
Addressing these wastes can be hugely beneficial to operations – and can actually result in doing less. What’s more, by paying close attention to where waste might be found, you may naturally discover areas where environmental effectiveness can be achieved.
How Steel Is Going Green
In 1950, 189 million metric tons of crude steel were produced globally, according to the World Steel Association.
Ten years later that amount nearly doubled to 347 million.
In 1970, 595 million, then 717 million in 1980, and 770 million in 1990.
At the turn of the century, the number rose to 850, then rose significantly by 2010 to 1,435 metric tons.
By 2020 the amount of crude steel produced globally was 1,879 metric tons.
There is plenty of steel being used to manufacture products of all types, as well as for construction and other applications, and that’s not going to change. The amount of steel used to produce things will grow.
But there’s a concern – one that even the World Steel Association, the preeminent steel industry association, recognizes:
“In 2020, on average, every tonne of steel produced led to the emission of 1.89 tonnes of CO2 into the atmosphere. In 2020, 1,860 million tonnes (Mt) of steel were produced, and total direct emissions from our sector were of the order of 2.6 billion tonnes, representing between 7% and 9%. of global anthropogenic CO2 emissions.”
Yes, there are significant amounts of emissions associated with producing steel in the traditional way: About 70% of steel is produced with the blast furnace-basic oxygen furnace approach. The blast-furnace approach is based in transforming iron ore into pig iron using coke – which is made from coal – as fuel.
There are some innovations in steelmaking that are being pursued, such as using green hydrogen to provide energy.
Carbon Free
Another innovative method is being developed by Boston Metal, a company that spun out of MIT 10 years ago. The company’s director of communications, Dawn Kelly, says the goal is to license the company’s molten oxide electrolysis (MOE) method to steelmakers by 2026. The approach is elegant in its simplicity. It takes carbon out of the process.
There is a containment vessel that includes an inert anode. That anode is immersed in an electrolyte that contains iron ore. Electricity (ideally produced from sustainable sources) is applied to the anode, and iron ore is added to the vessel. Kelly says, “We can use all grades of iron ore, not just the premium grades needed by other processes.” The anode heats the material to 1,600 degrees Celsius, at which point the electrons split the iron ore so there is molten iron, which falls to the bottom of the vessel from which it is removed, and the oxygen is vented from the top.
Chemically:
Fe2O3 + eˉ = Fe + O2
No carbon.
Kelly says the process has been validated at lab scale and they are in pilot for the inert anode to operate at production levels. Realize there is not only the tremendous heat the anode must withstand but a corrosive environment in that vat, given the oxygen. What’s more, that anode has to last for an extended period of time. Consequently, there is significant metallurgy going on at Boston Metal to produce that anode.
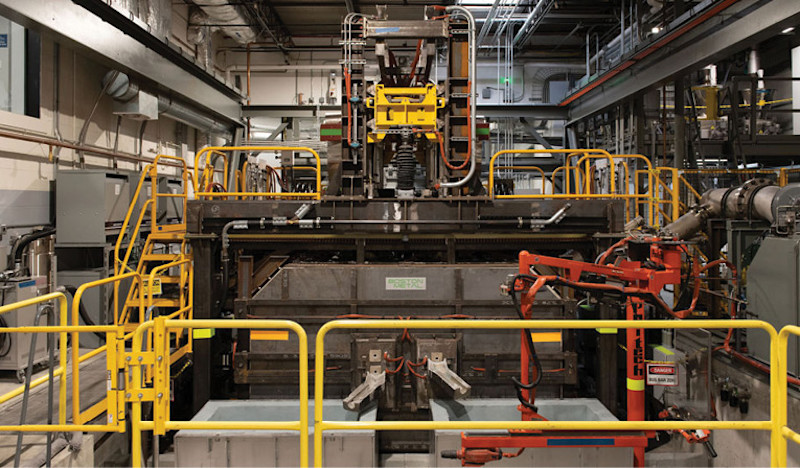
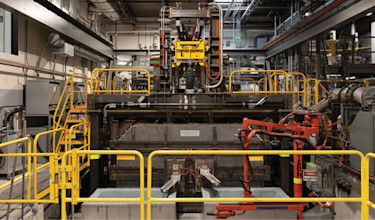
Inside Boston Metal: molten oxide electrolysis for the production of iron without carbon emissions. (Image: Boston Metal)
Asked whether the traditional steelmakers have any interest in what they’re doing, Kelly points out that leading global steel company ArcelorMittal is an investor in the company. As is BMW, so there is an interested user of the end product.
Soon, it seems, the bar stock or sheet being processed in manufacturing operations may be a whole lot greener than it historically has been.
To read the rest of the Energy Issue of MT Magazine, click here.