Building Better Leaders
Companies have no control over unpredictable tariffs and geopolitics. As manufacturing leaders navigate the best approach to responding to new global trade developments, workforce training stands out as a clear, fully controllable competitive advantage. A strong, skilled workforce is key to reshoring and manufacturing growth as well as being responsive and competitive enough to minimize the impact of global change.
Apprenticeship training provides a clear path toward this goal. Within the apprenticeship framework, companies experience reduced turnover and better recruitment, gain a talent pipeline of skilled workers, develop future managers, and increase global competitiveness and reshoring preparedness.
In Part 1, Part 2, and Part 3 of this series, we shared the stories of individuals and companies who have used apprenticeship training to forge lasting careers and shape the next generation of industry leaders. We showed that a university degree is not an indispensable criterion or, at least, not a required first step to achieving career success.
In Part 4, you will meet some famous and not-so-famous leaders who started as apprentices. Famous or not, their apprenticeship training influenced their outstanding leadership.
Jason Woodard, Geislinger Corp.
Meet Jason Woodard, the chief operating officer (COO) of Geislinger Corp. Woodard leads manufacturing, human resources, quality, project management, and manufacturing engineering functions, ensuring operational excellence and strategic growth. He holds a bachelor’s degree in business from Baker College in Jackson, Michigan, and an MBA from Cornerstone University in Kalamazoo, Michigan.
Woodard began his successful career with apprenticeship training as an industrial maintenance mechanic at Hillsdale Tool & Manufacturing Inc. in Hillsdale, Michigan, from September 1996 through June 2000.

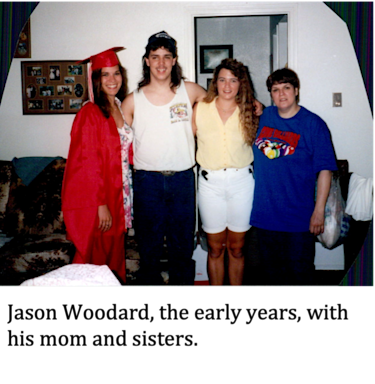
Woodard recounted the importance of his experience:
“My apprenticeship was a turning point in my life – it was the first time I truly loved learning. I gained both theoretical knowledge and hands-on experience, guided by journeymen with decades of expertise. This combination of structured education and practical application gave me an immense sense of pride in my work, making me eager to show up every day and improve my craft.
“Apprenticeships provide an unparalleled foundation for a career in manufacturing. Nearly 25 years after completing mine, I still apply what I learned daily as a COO. Apprenticeships allow individuals to develop real-world skills while learning alongside seasoned professionals – something that simply can’t be replicated in a traditional classroom.”
Paying It Forward
Woodard explained why he feels such an intense appreciation for apprenticeships and what he’s doing to pay it forward: “Because I’ve personally experienced the value of an apprenticeship, I’ve made it a priority to develop new opportunities for the next generation. At Geislinger, I’ve had the privilege of leading the creation of three new apprenticeship programs, and today, approximately 13% of our hourly workforce is enrolled as an apprentice.”
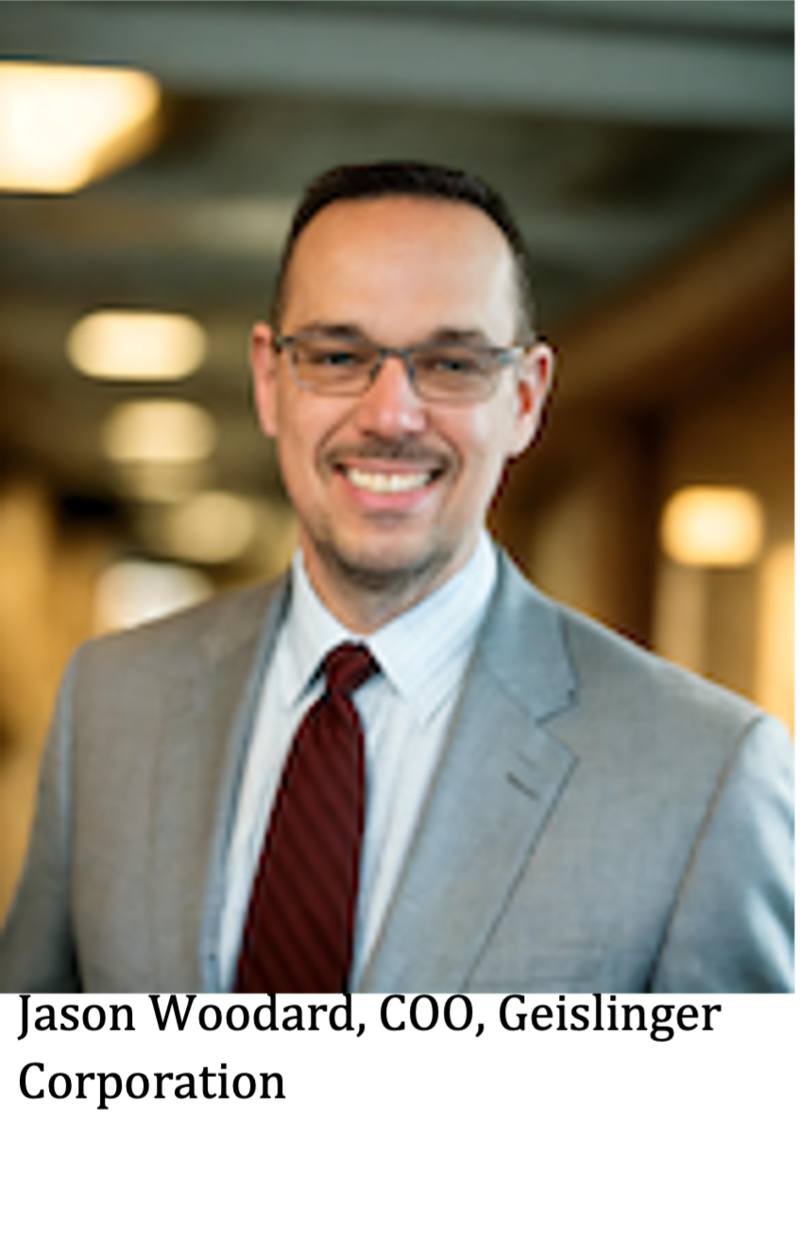
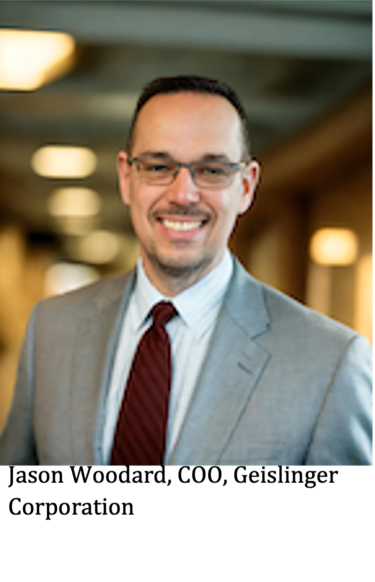
Woodard says his apprenticeship training has been invaluable.
“My career progression has led to compensation that exceeds the national average for Ph.D. and professional degree holders. Today, I remain actively engaged in manufacturing as COO of Geislinger Corp., overseeing a company that designs and manufactures critical components for high-performance powertrains.”
Manuel Merkt, Haimer USA
Next, meet Manuel Merkt, COO and vice president of marketing of Haimer USA. Merkt was born and raised in Germany and began his career in 2000 at the age of 16. He earned his 3-1/2-year dual apprenticeship as an industrial electrician at Maschinenfabrik Berthold Hermle AG, a leading manufacturer of high-end 5-axis machining centers and automation solutions. After completing his apprenticeship, he worked in machine assembly, installing electrical components and wiring Hermle machines.
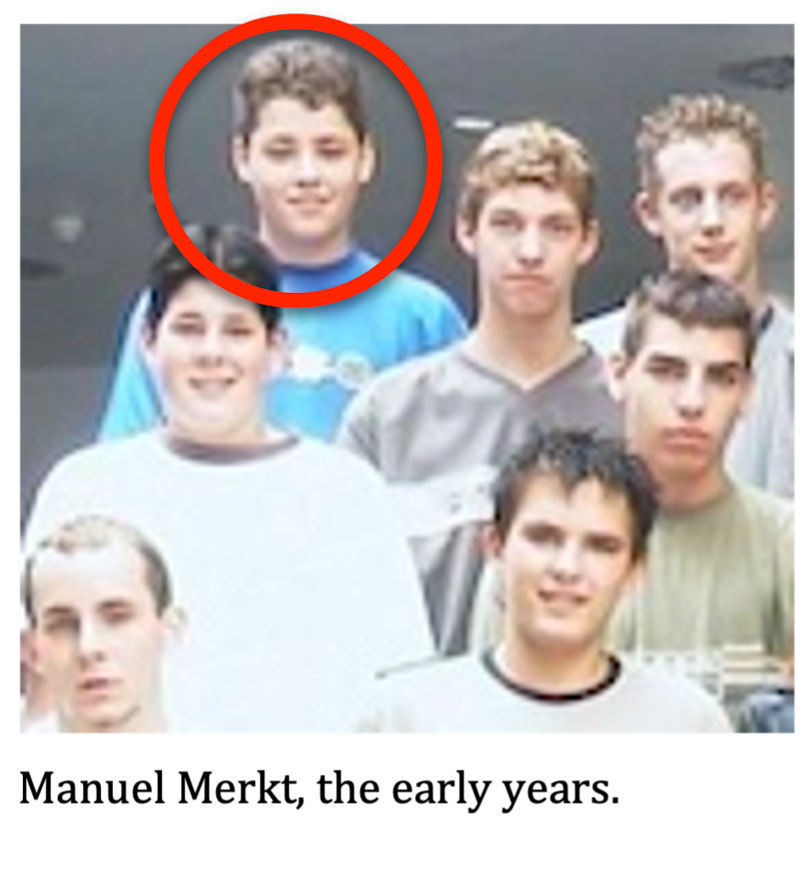
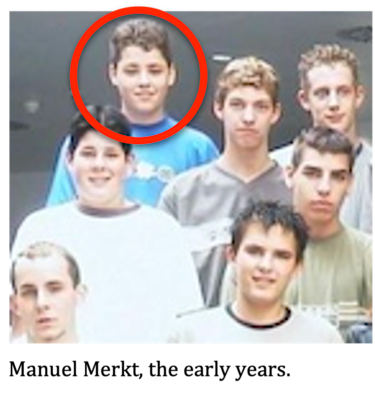
A year later, Merkt returned to school to gain his technical college entrance qualification. Shortly after, he started his journey toward a bachelor of engineering degree at the University of Applied Science in Constance, Germany, supported by a scholarship from Hermle. During his studies, Merkt gained hands-on experience across various departments at Hermle. He also spent nine months in Coventry, England, to enhance his English language skills and earn a Bachelor of European Engineering from Coventry University.
In 2009, Hermle offered him a three-month internship at their U.S. headquarters in Franklin, Wisconsin, providing valuable insight into the U.S. machine tool market. After graduating in 2010, Merkt moved to the United States and took on the executive assistant role at Hermle's North American headquarters. His deep product knowledge and strong connections to the German headquarters helped him rapidly advance within the company.
By 2014, Merkt became operations manager; in 2016, he became the executive vice president of operations. In 2018, he was promoted to president and COO, leading Hermle USA’s executive team. He also served on the boards of the German-Immersion Foundation of Milwaukee, the Franklin Business Park Consortium, and the German American Chamber of Commerce of the Midwest, where he chaired the Skills Committee. He played a key role in bringing the ICATT apprenticeship program to Wisconsin, inspired by the German system he had experienced firsthand.
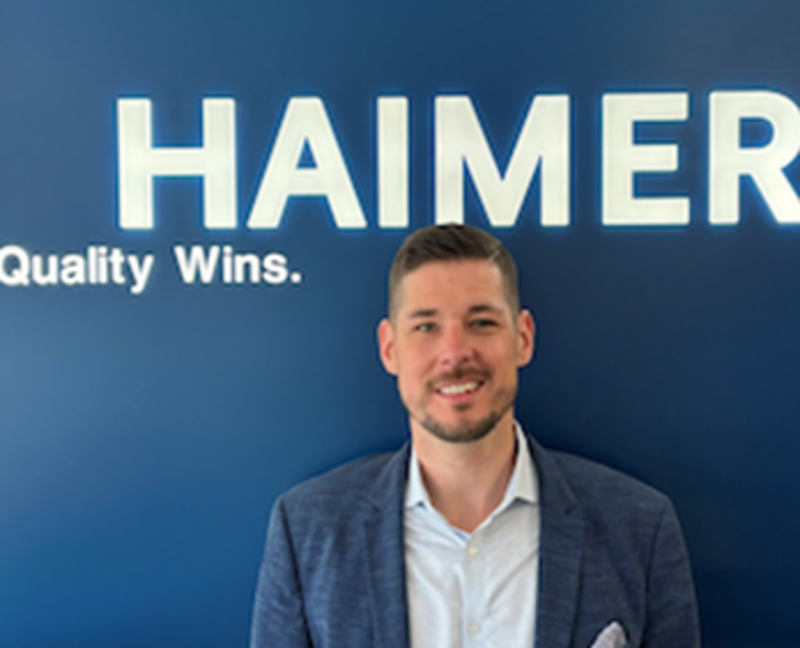
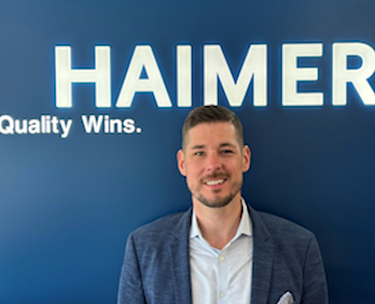
Manuel Maerkt, COO and Vice President of Marketing, Haimer USA
Recognized as one of Milwaukee’s 40 Under 40 in 2019, Merkt earned acclaim for his leadership and contributions to the community. After nearly 22 years at Hermle, he transitioned to Zund America in 2022 as president, leading the North American team for the Swiss digital cutting machine manufacturer.
In 2024, Merkt returned to the metal cutting industry, joining Haimer USA as COO and vice president of marketing, overseeing the North American subsidiary of the German manufacturer known for tool holders, cutting tools, and technologies in shrinking, balancing, presetting, and 3D measurement.
Famous Industrialists Who Started as Apprentices
Lt. Gen. William Signius Knudsen
Woodard and Merkt are in good company. Some of our most famous industrialists started their careers with apprenticeship training. William Signius Knudsen, born in 1879, was a Danish-born American auto industry executive and American general during World War II. Knudsen began his impressive career as a teenager, earning an apprenticeship at a bicycle shop, where he assembled the first tandem bicycle in Denmark.
Knudsen emigrated to the United States in 1900 and worked for Ford from 1911 to 1921, where he began supervising the establishment of Ford’s assembly plants during the development of the modern assembly line and mass production. Knudsen went on to serve as the president of General Motors Corp. from 1937 to 1940.
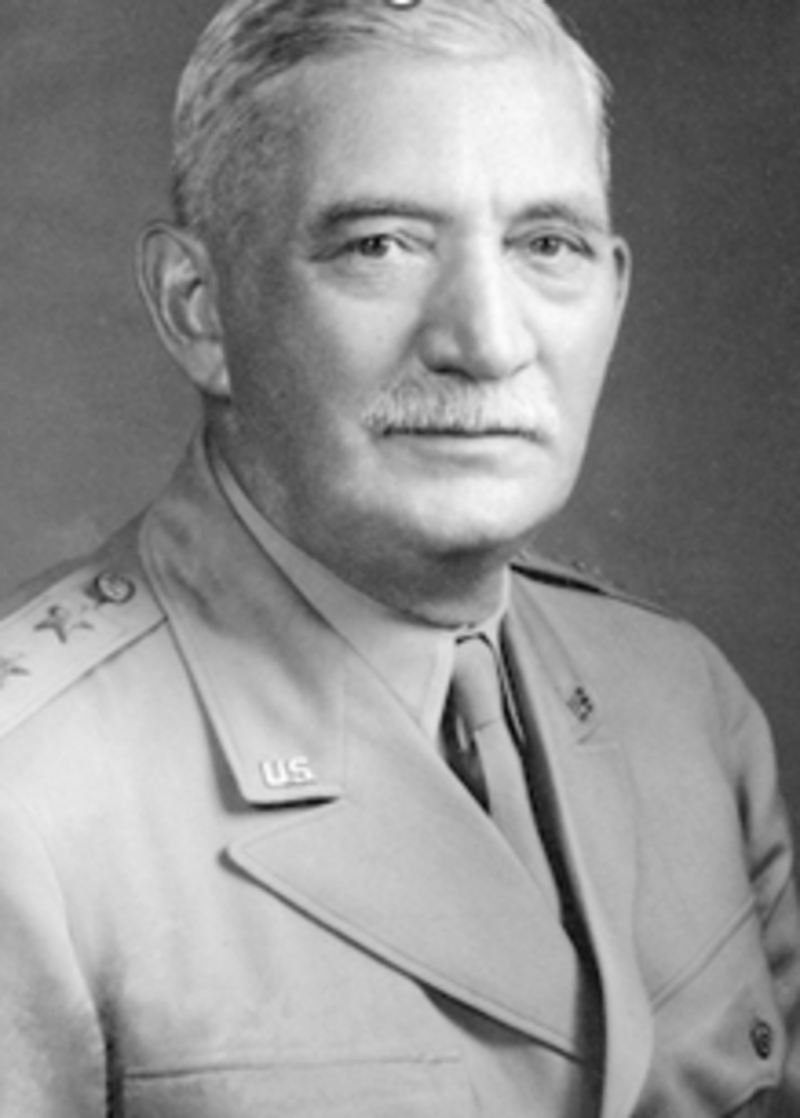
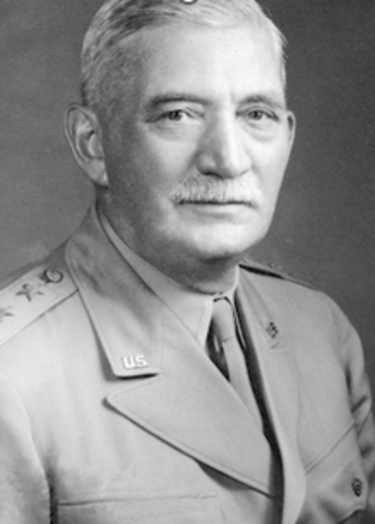
Lt. Gen. William Signius Knudsen
Knudsen’s vast expertise and success in production led the Franklin D. Roosevelt administration to commission him as a lieutenant general in the U.S. Army, where he directed the government’s massive armaments production program during World War II. In July 1944, he became director of the Army Air Forces Material and Services unit and earned the Distinguished Service Medal for “expediting the production of aircraft, guns and other munitions.”
Is College Still Worth It If You Can Pass an Apprenticeship?
Many industry leaders we have covered have combined a college degree with apprenticeship training. The combination can provide a practical basis for theoretical studies, increase job opportunities, make you a more competitive job contender, and lead to faster career advancement. Also, the apprenticeship training may cover some initial college tuition fees, saving students significant money.
Share Your Apprentice-to-Leadership Story
If your path to success started with an apprenticeship program, please consider contributing to our “Industry Leaders Who Started as Apprentices” series. Share your story with us at this link to promote manufacturing apprenticeships nationwide or contact me at harry.moser@reshorenow.org.
Are You Thinking About Reshoring?
Let’s collaborate to support skilled workforce development and rebuild the U.S. manufacturing base. For help, contact me at 847-867-1144 or email me at harry.moser@reshorenow.org. Our main mission is to get companies to do the math correctly using our free online Total Cost of Ownership Estimator (TCO). By using TCO, companies can better evaluate sourcing, identify alternatives, and even make a case when selling against imports.
Have you reshored a metal component or product? Apply for the National Metalworking Reshoring Award today. Applications are due by June 30, 2025.