If Paul Ericksen managed the supply chain, could Rome have been built in a day?
But seriously, Ericksen has some colossal achievements, notably as part of his 30-year-career with John Deere and the launch of its tractors into The Home Depot. Ericksen has worked as chief procurement officer at a Fortune 300 company, headed a Department of Defense supply chain flexibility initiative and founded his own executive-level consulting firm. Today, he writes one of the best-read monthly columns for IndustryWeek.
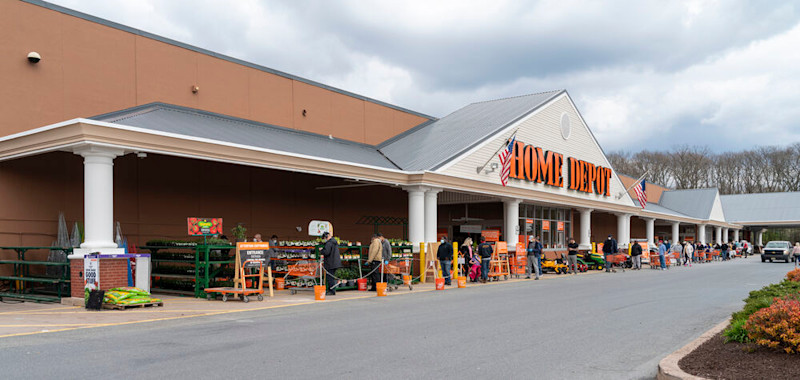
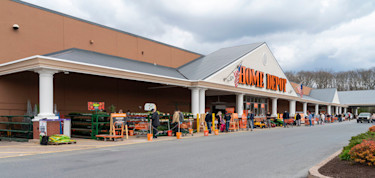
A tireless advocate for lean supply chain principles, Ericksen recently shared his wisdom in an IMTS spark session. Here are 10 thought-provoking details from his 60-minute interview, titled Changing the Game: Lean Supply Chain Performance, that can benefit both OEMs and suppliers.
The Home Depot holds minimum product and so require almost instantaneous replenishment. Deere could have built a huge finished product inventory—at a cost of $890 million dollars—or it could have a lean supply chain. Guess which strategy enabled Deere to double projected sales while satisfying 97% of demand?
Lean supply chain performance requires having a critical mass of strategic suppliers who can react to changes in demand—such as to the ability to supply 20 percent more parts than are in the rolling schedule with just two weeks’ notice.
Purchasing managers who make names for themselves by outsourcing to low-piece price countries cannot capitalize on spikes in consumer demands. The perennial shortage of this year’s “must have” Christmas toy is the perfect example.
A Japanese automotive manufacturer with a plant sited in the U.S.A. has a strategy of sourcing “locally.” A few years ago, 96% of annual spending was with suppliers located within 200 miles of their primary assembly facility.
Match the typical days-on-hand of pre-built inventory required at dealerships to maintain customer fill rates to the corresponding car manufacturer: 100, 50, 43; GM, Toyota, Subaru.
What is the better executive metric: chasing the lowest piece price around the globe or implementing lean supply chain practices that reduce day-on-hand inventory by 50 days?
Do not regard logistics as a major contributor to lean supply chain performance. Logistics and warehousing are Band-Aids needed to mediate improper source selection.
Facilitating transfer of best practices to suppliers — such as reducing the need for both supplier and customer part inspection — contributes to having a lean supply chain.
It took seven years to transition from an inspection-based to process capability-based quality program, but, in doing so, Deere was able to go from 29 inspectors down to three, freeing 26 people to work in other areas of the factory.
There’s no OEM that can be world-class unless they source from world-class suppliers.
Visit imts.com/spark to view the full session and see other supply chain-related content.