By IMTS
November 11, 2020
Professor Eric Wooldridge is passionate about teaching CAD-CAM and 3D Printing at Somerset Community College(SCC) in Somerset, Ky. He encourages mistakes because, “That’s how students improve.” He is implementing the state’s first Rapid Response Additive Manufacturing Initiative (RRAMI), an effort he introduced in April 2020 while he coordinated a Herculean effort to 3D-print Personal Protection Equipment (PPE) for first responders dealing with the COVID-19 crisis. With aerospace manufacturers and defense contracting industries adopting AM, RRAMI might be one of the Bluegrass State’s most promising investments.
In March of 2020, like many in the AM community, Professor Wooldridge worked tirelessly to print and assemble Personal Protection Equipment (PPE), such as headbands and face shields, to help front-line and healthcare workers in his state. Despite numerous challenges—like finding transparencies for the face shields and organizing volunteer assemblers—his team came up with creative approaches to produce 7,000 face shields and deliver nearly 6,000 of them in just six weeks—achieving an average of 300 per production day.
In the midst of 3D printing and fulfilling orders, he thought, if only the other community colleges in the Kentucky Community & Technical College System (KCTCS) had AM centers, they could be aiding in the effort to fight COVID-19 and fulfilling a supply chain gap.
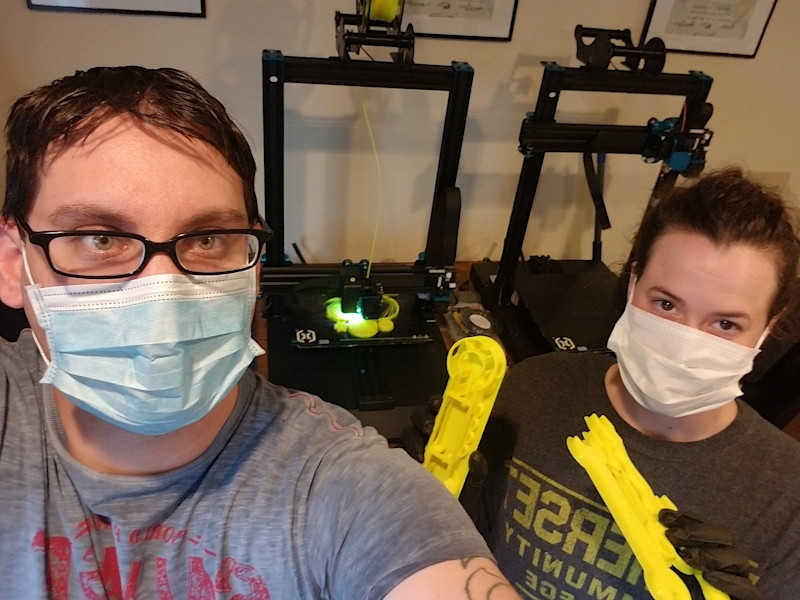
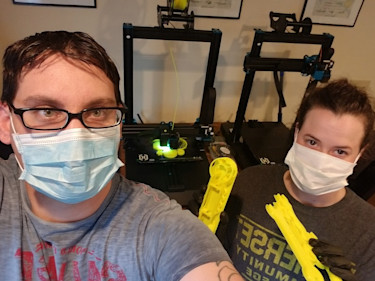
In early-April, when it became clear that in-person classes and training would not resume, Somerset’s Director of Grants, Elaine Kohrman, and KCTCS’s Executive Director of Professional Development and Innovation, Paige Brooks-Jeffiers, contacted Wooldridge for ideas about spending the surplus budget in KCTCS. Wooldridge responded with his idea to implement a Rapid Response Additive Manufacturing Initiative (RRAMI) at four of Kentucky’s other fifteen community colleges.
KCTCS’s administration quickly approved RRAMI for multiple reasons. It could see how Professor Wooldridge’s AM lab quickly filled gaps in the manufacturing supply chain for critical PPE in their state. It also recognized the benefits of AM for a quick response for local on-demand manufacturing and its growing adoption by local aerospace manufacturers and defense contracting industries.
“RRAMI is a win-win for KCTCS, students, business, the economy, and Kentucky’s future,” says Wooldridge.
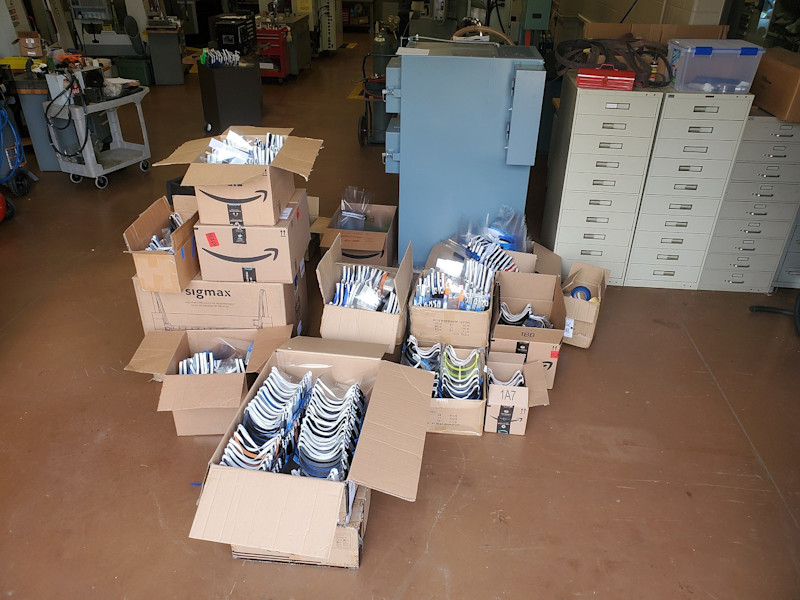
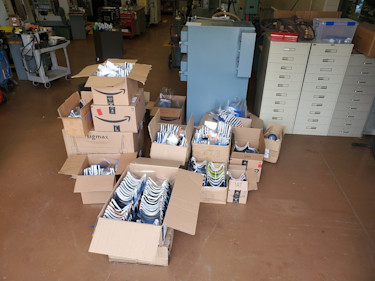
In return for the AM training and equipment, the new sites offer a 3D Printing Technician certificate to students as well as the ability to join in responding to future crisis events, such as natural disasters, terrorist attacks, or infrastructure breakdowns. Professor Wooldridge developed the certificate program, which is 16-18 credits and designed to complement any industry that can benefit from additive manufacturing including art, design, welding, CNC, engineering, biomedical, surgical technology, materials development, and culinary arts.
“We are thrilled to be training and setting up RRAMI across the state. Not only will we be able to respond quickly in the production of desperately needed products in times of crisis, but we will be preparing more students for careers in a variety of business sectors including advanced manufacturing for the aerospace, auto, and defense industries,” says Wooldridge. “These sectors depend on a skilled and creative workforce and are vital to the prosperity of Kentuckians.”
“In the next decade, the market potential for AM is estimated to grow significantly,” says Wooldridge. (Fortune Business Insights states, “The global 3D printing market size stood at USD 8.58 billion in 2018 and is projected to reach USD 51.77 billion by 2026.”1)
“Kentucky’s most significant export is aerospace, and our state has many manufacturers that contract with the U.S. Department of Defense. Data shows that both sectors are heavily investing in additive manufacturing because of its capability to reduce part production and produce next-generation products that are more complex and lightweight,” says Wooldridge.
“We have helped multiple companies begin to harness the savings and opportunities in additive manufacturing. Our students are currently employed where AM is applied,” says Wooldridge.
What’s Next? Professor Wooldridge’s energy and enthusiasm for AM is inspiring. While teaching and implementing RRAMI, he is also working with a University of Kentucky chemical and materials engineering team to develop a face mask with a 3D-printed membrane-filter that inactivates the coronavirus.
With funding and support from Kentucky's National Science Foundation (NSF)-sponsored Established Program to Stimulate Competitive Research (EPSCoR), the UK-SCC team is 3D printing the substrates, made of polypropylene, in a honeycomb pattern to allow for a strong, breathable structure.
With AM taking off throughout Kentucky’s community colleges, a growing talent pool will be ready to help drive the state’s driven by competitiveness and innovation.
See what else Professor Wooldridge is doing, follow him on his AM Lab Facebook page or LinkedIn.
IMTS Spark
Want to learn more about AM and other technologies transforming the advanced manufacturing industry? Check outIMTS spark.