Collaborative robots – or cobots – have been used in manufacturing for about two decades. Cobots are specifically designed to interact with humans in a shared workspace and therefore minimize the risk of accidents or injuries. They are equipped with sensors to avoid collisions and ensure passive compliance in the event of unplanned contact. Cobots are relatively lightweight compared to industrial robots and are usually portable.
“Robotics and automation have become foundational to the evolution of the manufacturing industry, and now cobots have emerged as the newest area of innovation and productivity,” said Stephen LaMarca, technology analyst, AMT. “Although cobots are not as fast or powerful as traditional industrial robots, as they are force limited to 15 Newtons, their much greater level of safety offsets limitations in force and speed.”
Advances in sensors, artificial intelligence (AI), machine vision, and light detection and ranging (LiDAR), among other technologies, are making cobots easier to program, less expensive to deploy, and increasingly flexible in the types of tasks they can safely perform. According to the International Federation of Robotics, cobots are the fastest growing segment of the industrial robotics sector and growing at a rate four times faster than that of traditional industrial robots. Analyst firm Emergen Research predicts that cobot sales will climb to $9.3 billion by 2027, up from $0.7 billion in 2019.
“Cobots are also ideal for smaller manufacturers given their much lower price point and how much easier they are to program and use, reducing or eliminating the need for engineering staff and lost productivity due to downtime. In the near future, we see continued advances in edge computing as being important in equipping cobots with even greater flexibility and easier implementation,” added LaMarca.
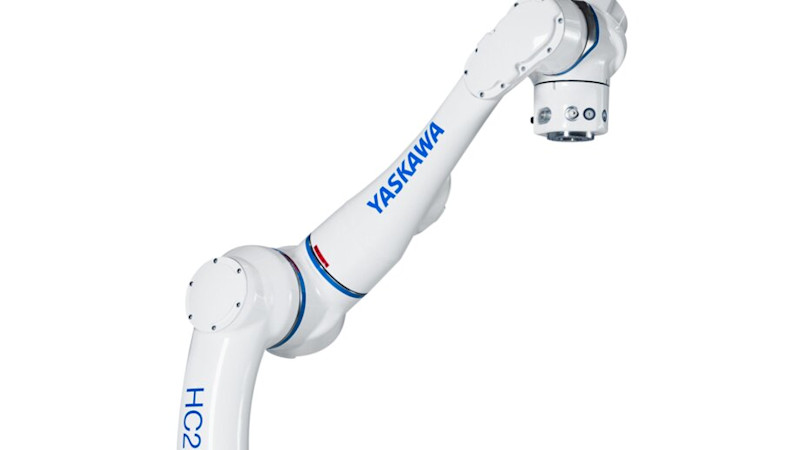
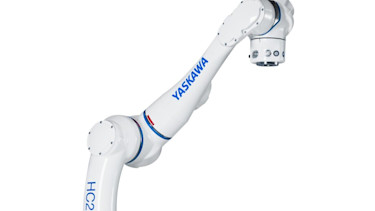
There are three main categories of safety assurance in cobot systems: speed limits, force feedback, and external sensing. ISO/TS 15066, first introduced in 2006, ensures that all machines classified as cobots require at least one safety feature, such as a safety-rated monitored stop, hand guiding, speed and separation monitoring, or power and force limiting. ISO/TS 15066, published in 2016, specifically addresses the new field of safety requirements for cobots in much more detail. Under TS 15066, the force and speed monitoring of the cobot is set based on application data, human contact area, and workspace hazards. Cobots are often allowed to operate at higher speeds when no persons are in the collaborative workspace or hazard zone.
Unlike industrial robots, cobots are relatively easy to program, even by workers with no knowledge of programming. Most use hand guiding – also called teaching by demonstration – in which the cobot learns while being guided through the sequence of movements needed to perform a task. The price of cobots, starting at about $25,000 and decreasing every year, makes them increasingly accessible for small- to mid-sized manufacturers.
A few additional facts about cobots:
Cobot applications need not feature collaboration, nor does safety need to be a factor. While cobots are engineered to work safely alongside people, collaboration with humans does not always figure into their value.
Cobots are not ideal for lifting heavy items, doing work in very dirty or hazardous environments, or performing tasks that require the accuracy of industrial robots, such as high-volume mass production.
Cobots are a great fit for a variety of applications, including machine tending, metrology, assembly, screwdriving, visual inspection, packaging, and palletizing.
Cobots are currently designed for payloads less than 75 pounds and they are not as fast as traditional industrial robots.
Watch a quick video of cobots in action here.