Ever wonder why everyone seems to have a different definition and description for digital manufacturing? The answer is straightforward: There is no one standard definition for digital manufacturing that can be applied across other businesses or facilities. Just as every business or facility has its own unique characteristics, the application of digital manufacturing strategies applied in that business or facility should be equally unique. The fact is, everyone is already doing some version of digital manufacturing, whether they call it that or not.
In its simplest form, digital manufacturing uses electronic information collected from or related to a manufacturing operation to support more informed decision-making and increase the efficiency of personnel and other resources.
The key to building your unique digital manufacturing strategy is to leverage an array of technologies that deliver a sustainable and scalable solution. The best way to achieve such a solution is to leverage a combination of industry standards and “business-specific” standards to build your decision-management strategy. Simply throwing technology at your facility without an integrated strategy will increase costs, lower benefits, and cause premature obsolescence.
A digital manufacturing solution can be envisioned as layers of interdependent technologies that can be integrated to form a unique solution for each business or facility.
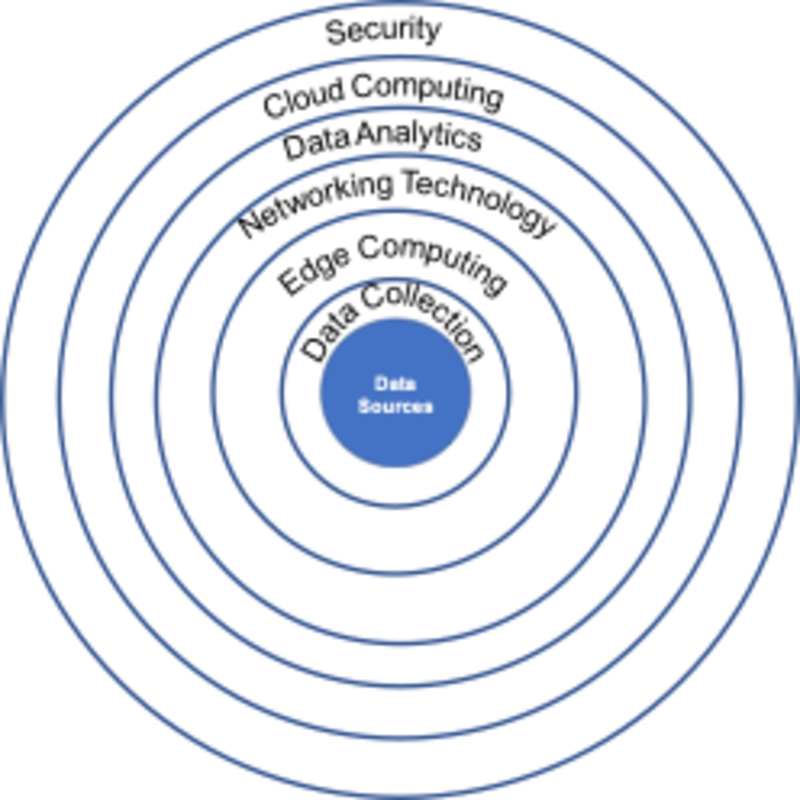
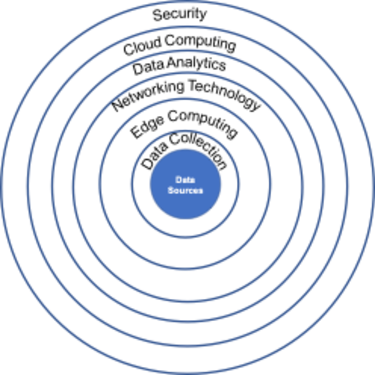
How do you deploy a sustainable solution that will adapt economically to the ever-changing technologies available in the computing and information management world? One option is to develop a deployment strategy where each layer in the data collection system is implemented as a unique and separate function. Each layer should then have a standardized interface to both the layer below and the layer above – essentially a set of standardized building blocks. Such an architecture allows a company to replace or upgrade any portion of the system that does not function as anticipated, becomes outdated, or fails with minimal impact on the balance of the system.
We have all heard of the pain and expenses companies have experienced when replacing significant portions of their information management systems – whether an accounting system, ERP system, or MES system. The ability to upgrade/replace smaller parts of a system has a lot of benefits.
Regarding your manufacturing support systems, the system model described above can provide the agility needed to respond to ever-changing business situations. One example of a relatively recent shift in reality that impacts all manufacturing facilities and causes companies to reassess their information management systems is the explosion of cybersecurity threats. The security functions of the past deployed in our manufacturing operations must be hardened. Response to these attacks impacts more than simply upgrading the outer security layer of your information management system – the manufacturing shop floor does not live in a protective bubble. Just as many cybersecurity attacks (intentional or unintentional) are initiated from within a business as are initiated from outside actors. Every layer of your system architecture needs to be hardened. You can learn more about addressing cybersecurity threats in AMT’s series of papers, “Building an Advanced Cybersecurity Plan.” A modular system architecture makes deploying extensive security enhancements at multiple levels in your system much more practical.
Another situation that is driving a whole new series of innovations needed in manufacturing information management systems is the recent pandemic. Companies are looking to their information management systems to support the ability to quickly adapt to new market demands, maintain production with minimal personnel, and have the flexibility to redeploy equipment for the production of alternative goods and products. Again, a modular information management system will make deploying system enhancements faster and more cost-effective.
Agility to adapt to the ever-changing business environment is critical to a company’s future success. A competent and adaptable information system is crucial for maximizing manufacturing resources.
You can learn more about deploying a modular digital manufacturing information system in AMT’s “Digital Manufacturing” white paper series.