It has 320,000 employees, generated $85.87 billion in revenue in fiscal year 2023, makes products ranging from computerized tomography devices to smart infrastructure systems – and was established in 1847 in Berlin, based on the invention of the pointer telegraph (a device that improved the transmission of messages when there weren’t ones and zeros but dots and dashes) by Werner von Siemens.
Few companies (Corning, GE...?) have lasted as long as Siemens.
And few have the kind of relevance that Siemens has, with its focus on industry, infrastructure, transport, and health care, all predicated on digitization and decarbonization.
Not only are those two pillars – digitization and decarbonization – things that its products, software, and systems help its customers achieve, but they are key elements throughout Siemens’ various lines of business.
Actual Advantage
Consider this: In Nanjing, China, Siemens had three production sites for its R&D, production, storage, and logistics for its CNC business of building controllers, motors, and drives. It recently consolidated all three sites into a single “lean and green digital native factory.”
The greenness takes the form of annual energy savings of 5,000,000 kWh of energy, 3,300 metric tons of carbon dioxide, and the reduction of 6,000 cubic meters of water use.
Its leanness is evident in a 20% increase in productivity.
And the factory was first “built” as a digital twin, which helped make these achievements possible.
What’s interesting about Siemens is that it not only provides the tools that its customers use for digital manufacturing but also employs those same tools in its own product and process development and, importantly, execution.
As Raj Batra, president of Digital Industries for Siemens USA, puts it: “We’re one of the biggest manufacturers in our own right, so we feel all the pain that our customers feel.”
He points out they have manufacturing operations that are in need of modernization and digitalization; they have manufacturing operations that have quality rates of 99.9%, a DPM of 10 or 11, and the ability to handle hundreds of product variations a day.
So, they are working to change what they need to and replicate what’s working well. And digital manufacturing is key.
But what is it?
Batra: “The integration and digitization of design of products and the digitization of the design of manufacturing processes.”
It’s a “convergence of digital and physical technologies.”
It’s something that, well, sort of sounds familiar to those who have been involved in manufacturing since the 1980s.
Then and Now
Once, the hot acronym was CAD/CAM/CAE: computer-aided design, manufacturing, and engineering.
Batra notes: “Eighty percent of manufacturing costs are predetermined in the design phase,” so the idea was to “design for production.”
So, while CAD/CAM/CAE would address that, “the tools weren’t there to do it.”
He explains, for example, that while CAD and CAE allowed for the development of part models of geometry and physical properties, these were essentially static models. How the part would perform in the physical world wasn’t something that was provided.
What’s more (or less) is that there was a tendency back then, due to a separation of the strong domains of the CIO team and the manufacturing organization, to have manufacturing take the product design and try to determine how to manufacture it. All of this was time-consuming, not particularly efficient, and most particularly expensive.
A key aspect that was missing is true integration between design, manufacturing, and engineering, as well as the ability to simulate all aspects – from the characteristics and function of the part (what if it is an alloy that was then reconfigured to be produced with carbon fiber?) to its operation on the factory floor (how many robots are necessary for material handling given the operational characteristics of the automation?).
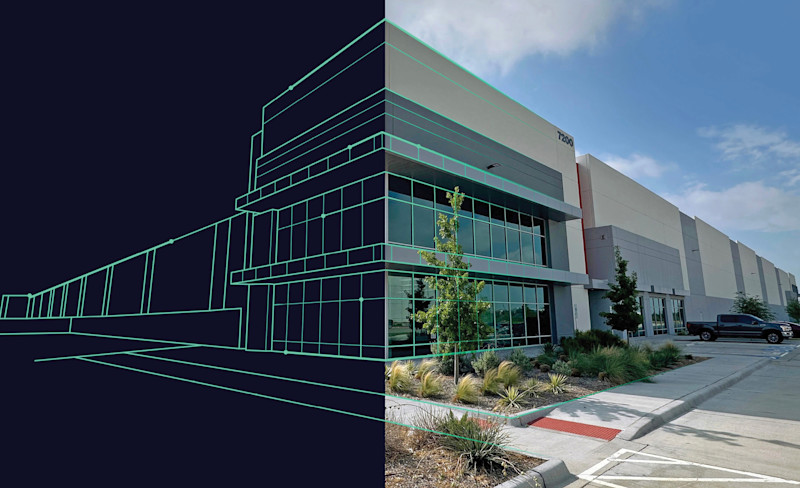
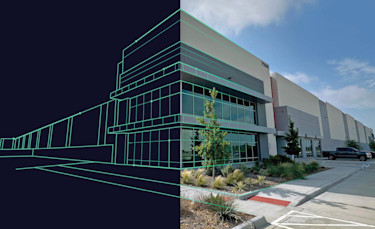
Siemens announced in November 2023 a $150-million investment in a new plant in Dallas-Fort Worth to produce electrical equipment for data centers. The company is using its digital twin and automation technologies for the construction and automation of the facility. That investment is part of $510 million being spent to build a new rail manufacturing facility in Lexington, North Carolina, and two electrical products plants - one in Grand Prairie, Texas, and the other in Pomona, California.
“When you simulate the product, you want the same capability and design tools to design the layout of the plant,” Batra says, adding, “You model the production process along with the design process and put them together on a common data backbone.”
The point is: Digital manufacturing, by its very design and nature, provides integration across the product and process development undertaking in a seamless manner and provides information about operational characteristics (of the product and the processes) not otherwise readily achieved. Of course, the big question is: How is this done?
“It always starts with good use cases,” Batra answers. “It’s not one-size-fits-all for people.”
He explains that, generally, in organizations, the domains of IT and manufacturing are strongly separated, and an MES (manufacturing execution system) or MOM (manufacturing operation management) – likely home grown – operates between them. To transform to a digital manufacturing environment, silos need to be eliminated and multidisciplinary teams created where everyone works with the same digital backbone.
One of the considerations, of course, is that unlike Siemens, which has developed its own full suite of software tools, most companies have software from various companies. So, just as the various job functions need to work collaboratively, Batra says that there is a need for interoperability between the various types of software in order to get the full value of an integrated digital manufacturing operation.
His point about good use cases for the deployment of this approach is based on the acknowledgment that many operations in the United States have been around for several decades, and there is a need to modernize them instead of using this as an opportunity to replace them with something brand new.
So, what he suggests is that by starting out by transforming a line or a part of a process and getting people from various functions to work together on this project, there is the ability to more quickly get an ROI, which then can help facilitate the execution of other projects.
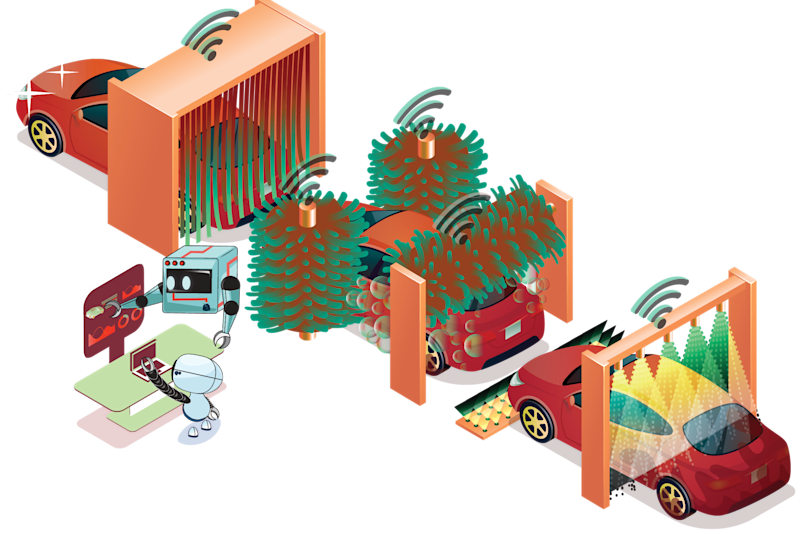
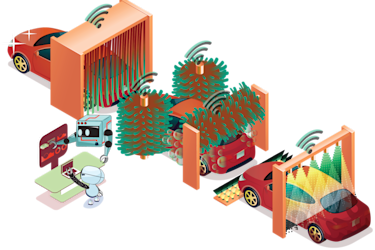
The Importance of Digital Manufacturing
Batra points out: “There’s never been more pressure to manufacture stateside than today.”
Some of the pressure takes the form of the supply chain snafus that were experienced during the past few years. Some of the pressure is positive, such as the billions of dollars made available by government initiatives for manufacturing.
A major challenge, however, is that much of the manufacturing infrastructure – equipment as well as people – is vintage compared to what’s happening in other parts of the world.
So, there needs to be a manufacturing renaissance that is based on not only digital design and simulation tools – and Batra emphasizes that this is product and process design and simulation, including the development of digital twins – but also on a workforce that is digitally savvy.
“Top executives need to advocate for this,” he says, citing the benefits of digital manufacturing, including:
• Cost advantages
• Competitive advantages
• Faster production
• Use of less material
• More mass customization
“It starts with that vision,” he says. “And then it needs to be pushed.”
Batra shares a surprising anecdote about software and automation use: “I’ve seen car washes that are using Industry 4.0 in a much more sophisticated way than some Fortune 500 companies.”
He explains that the car wash process is holistically designed such that the brushes are “smart,” providing information about how many vehicles have been processed as well as predicting when maintenance will be required. The system monitors the amounts of soap and water that have been used to help with asset utilization.
The PLC used is common to manufacturing. The automation systems bringing the vehicles through are similar. The network and software are analogous. But the difference is the vision to make the transformation and to minimize bureaucracy along the way. Nothing, Batra says, that can’t be advantageously undertaken by manufacturing operations of all types and sizes.
Werner von Siemens once said, “An innovation’s importance lies in its practical implementation.”
And that’s precisely the approach that needs to be taken by companies when it comes to digital manufacturing.
To read the rest of the Digital Manufacturing Issue of MT Magazine, click here.