Smart manufacturing revenue will grow substantially during the next eight years, from $4.5 billion this year to $51.5 billion in 2026.
This growth will hit all the revenue segments — including security, device and application platforms, connection, data and analytics, and networks — except for professional services revenue, which will drop from 31 percent this year to 13 percent in 2026. The reason for that drop is because as edge computing begins to augment the cloud, there will be less of a requirement for consulting on custom coding and systems integration. Simply put, it is going to get easier to deploy and scale most smart manufacturing technologies.
What’s the difference between edge computing and cloud computing? Edge computing is data processing at the edge of a network, whereas cloud computing is holding it in a central data warehouse. Balancing edge and cloud computing holds the potential to optimize smart manufacturing solutions. However, a major hurdle most manufacturers face is extracting data and networking equipment on the factory floor. That’s because there are operational technologies communicating with industrial ethernet proprietary protocols from individual OEMs to transmit data and information. The main challenge is getting OT to communicate with IT, namely Internet protocol HTTP, which is what the cloud uses. OT and IT really struggle to communicate and exchange data. Not only that, but OT also struggles to exchange or communicate data with itself. As these different protocols are propriety, they do not talk to each other.
On-premise computing deployments are still common due to concerns with privacy, security, and sometimes regulatory compliance, but there has been a significant rise in demand to implement cloud computing, which has almost unlimited computing power at about half the cost. Yet there are still challenges facing the cloud, mainly increases in the “Vs of Big Data”: volume, velocity, and variety of sensor readings — e.g., acoustic or video — that lead to increasing cloud costs for storage, processing, and transporting data. The solution is workload consolidation onto edge gateways and servers that can process streams of data on-premise and then feed that up to the cloud for further storage, analytics, and training models. These edge solutions can deal with those multiple devices from multiple manufacturers if they use the right solutions.
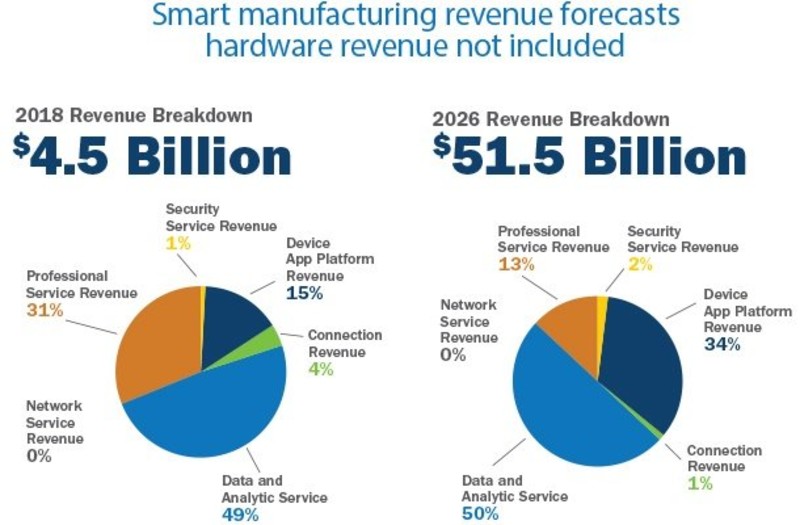
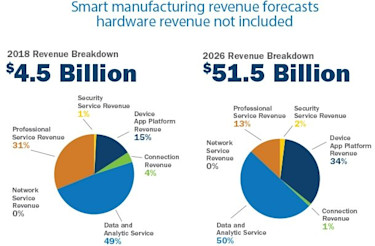
Using edge in conjunction with cloud to augment the cloud increases the capacity of data processing while decreasing the volume of data sent to the cloud, therefore, lowering the total cost of ownership.
The stream processing side of edge computing is huge because it empowers the user to catch anomalies in the data that batch data to the cloud will miss. When you have sensor readings every millisecond, there are going to be blind spots and jitters in batch data to the cloud. Which means, if you can process that on an edge gateway or server, you can use the stream processing much more effectively for executing predictive maintenance or quality control. The challenge for both vendors and end users is deciding what to publish to the cloud and what to process at the edge. But ultimately, the vendors must give this control to the end users to allow them control over their own data. Another challenge is minimizing that custom code at the edge.
We are seeing more edge intelligence from different IT vendors due to demand from end users for more edge capabilities, as they offer more of a traditional on-premise computing feel but with a lower total cost of ownership.
Recommendations: Edge vs. Cloud To flexibly adapt to customers’ needs and help them scale, smart manufacturing vendors must:
Implement architectures that have stream processing on-premise so you can take advantage of the low latencies of edge computing, fewer blind spots, and jitters to catch those anomalies. Deploying models at the edge means catching failure predictions and detecting defects earlier, and more ease in finding their root cause.
Give the end-user control of what to publish to the cloud. Every factory has unique requirements. The CIOs of these enterprises need freedom of what to publish to the cloud and what stays at the edge.
Promote the ability as a vendor to extract data from equipment on the factory floor. The ability to merge data flows from different OEMs is huge. The ability to adapt and leverage existing infrastructure and protocol translation is incredibly valuable, and clients will struggle without those abilities.
Have code-free application development and logic configuration that can be deployed at the edge. If you can minimize the need for custom code, you can speed up development scalability and deployment to get more innovation from more people, not just the people who know how to code.
Following this strategic guidance to optimize the balance of edge and cloud computing will enable smart manufacturing vendors and their clients to implement scalable and cost-efficient solutions for processing data across the board.