Like most manufacturers, Peter Rathmann, the owner of Allis Manufacturing in West Allis, Wisconsin, has struggled to find and retain skilled workers. He realized traditional personnel sourcing methods weren’t working well, and cast a wider net by hiring an often-overlooked population: people with autism.
According to the Survey of Income and Program Participation conducted by the U.S. Census Bureau, approximately 54 million Americans have a disability, collectively creating a deep pool of potential workers who may not have previously been considered.
Uniquely Abled
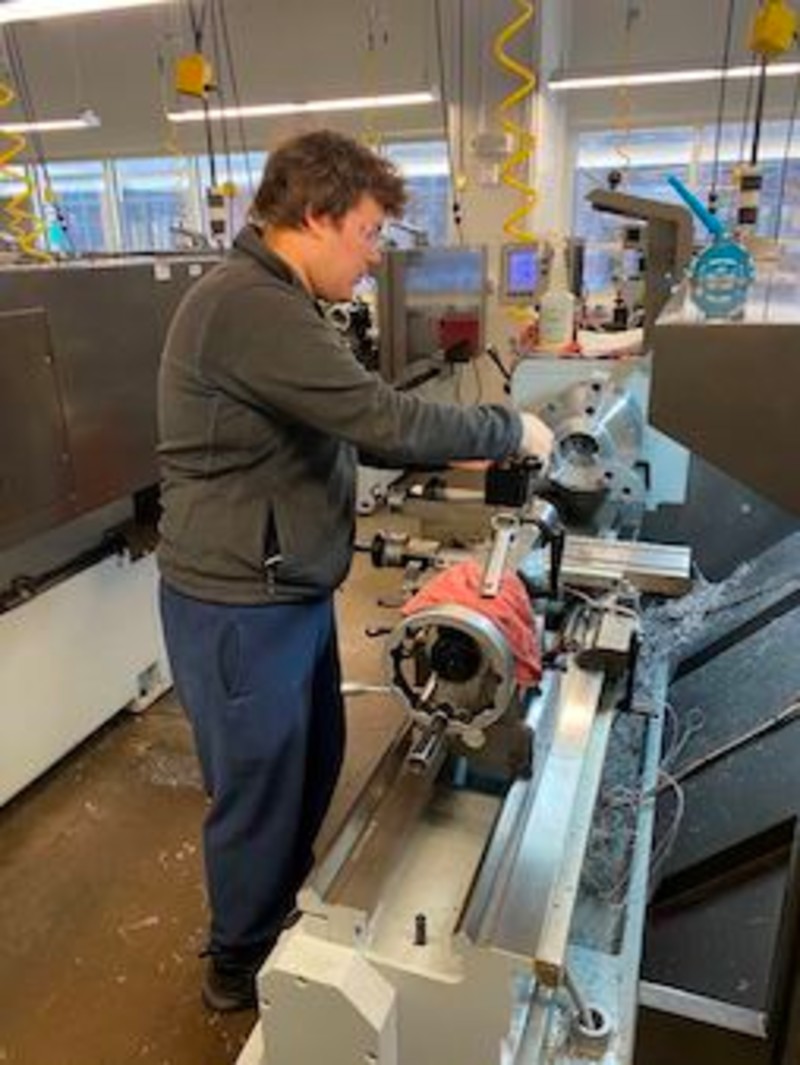
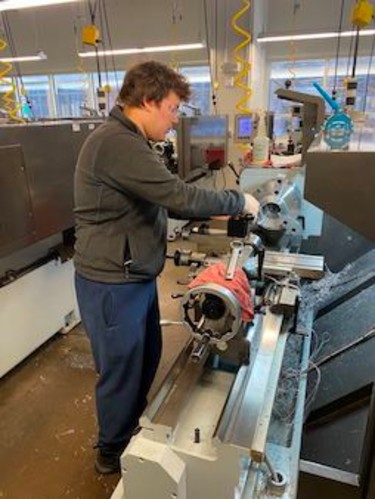
Recently, Rathmann hired 19-year-old Eric as a machining apprentice, and he immediately became a valued and productive member of the team. Eric is a graduate of The Uniquely Abled Project’s (UAP) Uniquely Abled Academy(UAA) at Milwaukee Area Technical College (MATC), a program that teaches CNC machining skills to people with autism.
“On his first day, we handed Eric a job print, taught him the basic control of the milling machine, and gave him a chance to see what he could do,” says Matt Petersen, an Allis Manufacturing machinist who trained Eric. “He converted everything to metric, plugged in all the information, and started running the machine by himself. We were surprised by what he could do.”
Founding the Uniquely Abled Project
Since 2013, the UAP, headquartered in Valley Village, California, has been providing CNC operator training, job placement, and support to people on the autism spectrum. The UAA at College of the Canyons in Santa Clarita, California, was so successful that eight colleges in six states have become Uniquely Abled Academies, and at least seven more are expected by the end of the year. So far, the program has graduated more than 130 people and achieved a nearly 100% job placement rate.
Inspired Father
As the father of two teenagers on the autism spectrum, Ivan Rosenberg was concerned about how his children would support themselves as adults. At that time, he was a business consultant for aerospace and defense manufacturers, and well aware of the labor shortages. He believed he could address those two challenges with a mutually beneficial solution and started the UAP.
A Team of Partners
The UAP partners with technical colleges, autism specialists, and state and local social service agencies to develop programs that properly train, place, and give ongoing support to autistic students for good-paying CNC operator jobs. But this program is not charity — it creates a pipeline of skilled talent that fills a major need for employers. In 16 weeks, a UAA teaches young adults to be entry-level CNC machinists and then provides job placement and post-hire support.
Highlighting abilities
The term “uniquely abled” was coined to focus on the amazing things that individuals on the spectrum can do. Forty percent of those with an autism diagnosis have above average intellectual abilities, and many have exceptional visual and academic abilities that make them a valuable contributor to the workforce.
“We’re shifting the perception of disability to highlight the unique abilities and extraordinary potential of our students,” Rosenberg says. “The abilities of many individuals with autism are a perfect match for CNC machining. They tend to be tolerant of repetition, detail oriented, able to focus for long periods, often mechanically inclined, and focused on accuracy. Plus, they tend to dislike transitions to different companies, so they are more likely to stay in a job they enjoy.”
UAP UAA Graduates Working Across the USA
Mike Bastine, director of the UAA at the College of the Canyons, sees first-hand how manufacturers in his area are now eager to accept UAA grads. A local high-tech medical device manufacturer has already hired nine graduates and asked for more.
Based on demands from local manufacturers, the UAA at College of the Canyons is expanding to add a four-week, fast-track robotic programming course. The training will teach programming basics and include hands-on learning. The University of California is providing the hardware — complete with robotic arms, sensors, conveyors, and other equipment to simulate a real manufacturing application.— complete with robotic arms, sensors, conveyors, and other equipment to simulate a real manufacturing application.
“Programming is more of an individual activity with one person and a computer, and it can be repetitive, which is an ideal match for our students’ skills,” Bastine says.
Growing in Popularity
The UAA at MATC, which started in 2021, has already graduated two student cohorts. For cohort three, which starts in the fall of 2023, they received 75 applications for 10 spots. The program contains much of the same training as MATC’s existing CNC course, with only slight modifications. The teacher uses language that makes more sense to the students, focusing on explicit direction without hyperbole or casual statements that could be taken literally. Also, the course adds some soft skills, such as social interaction in the workplace. Job coaches from the UAA accompany the new hires while they adjust to the job. As a result, employers often need little adjustment to their current onboarding process and the work environment itself.
Local Employers – Key to Success
Goldhmong Vang, coordinator for the UAA CNC Operator Program at MATC, cites the importance of relationships with local employers such as Allis Manufacturing who provide guidance on what machining skills are most relevant to teach, as well as other support.
“Our employer partners really help us build connections within the manufacturing field,” Vang says. “But they also let us know what skills the industry is looking for so we can make our students more valuable.”
Mindset Adjustment
With a daughter on the autism spectrum, Rathmann saw the potential for individuals with the same diagnosis and became an Advisory Board Member for MATC’s UAA program. He and his daughter travel around Southeastern Wisconsin telling manufacturers about the benefits of the program.
Rathmann’s advice to other manufacturers looking for talent is simple: “Take those long job descriptions, your traditional hiring pipeline, and the bureaucratic processes and just toss them out. If you find somebody that wants to work, cares about the work they do, and is willing to learn more, you are going to find a place for them. It takes a changed mindset to break down the traditional barriers of defining what makes a good job candidate.”
Learn more about the potential to tap into a new workforce on The Uniquely Abled Project website, with 16 centers across the country.
Smartforce Student Summit at IMTS 2024Explore the exciting career opportunities in advanced manufacturing by checking out IMTS.com/Smartforce which focuses on the Smartforce Student Summit at IMTS 2024 — a hands-on chance for young people to explore the latest technology in metal cutting, programming, design, robotics, automation, and more.