To help celebrate National Apprenticeship Week (November 13 to 19), AMT and IMTS are shining the spotlight on three equipment manufacturers training the workforce of the future through their apprenticeship programs. Some programs are well established but stepping up their game (Schunk, Okuma) and some are brand new (United Grinding). Our hope is other manufacturers can learn from their experience to start or expand their own apprenticeship program.
Learn from Germany
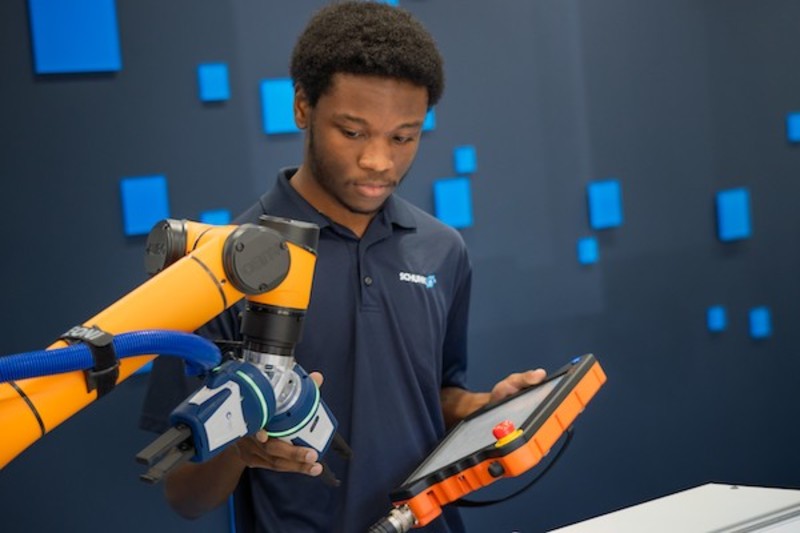
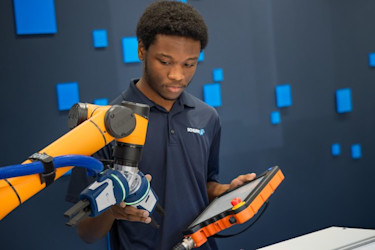
Schunk and United Grinding’s U.S. operations benefit from their company’s German/Swiss origins. Many of their employees have first-hand experience with the German/Swiss apprentice model, which is referred to as a dual vocational education system because students learn and work at the same time. Nearly 60% of Germans begin careers within the apprenticeship system.
While U.S. companies might not have an apprenticeship heritage, do not let that be a deterrent to starting a program, as every year of delay is another year without taking action to solve the skilled worker shortage.
“Just jump in the water and you will learn to swim. Will your first efforts be perfect? No, and that’s okay; you can adjust as you go,” says Andreas Brockmann, apprenticeship coordinator at United Grinding, Miamisburg, Ohio.
Brockman started the program in early 2023, set up the program in two months, and hired the first four apprentices two months later. Students attend Sinclair College two days a week, then spend three days on the job.
“Students get paid for a full 40-hour week with full benefits,” says Brockmann. The students will graduate with an associate degree in mechatronics, then spend another two years going from department to department mentoring under United Grinding’s application engineers.
In addition to being a German apprentice himself, Brockmann has also managed apprentice programs at other companies. So that others can benefit from his experience, he contributed to a report on bridging the German and U.S. apprenticeship models.
Find good partners
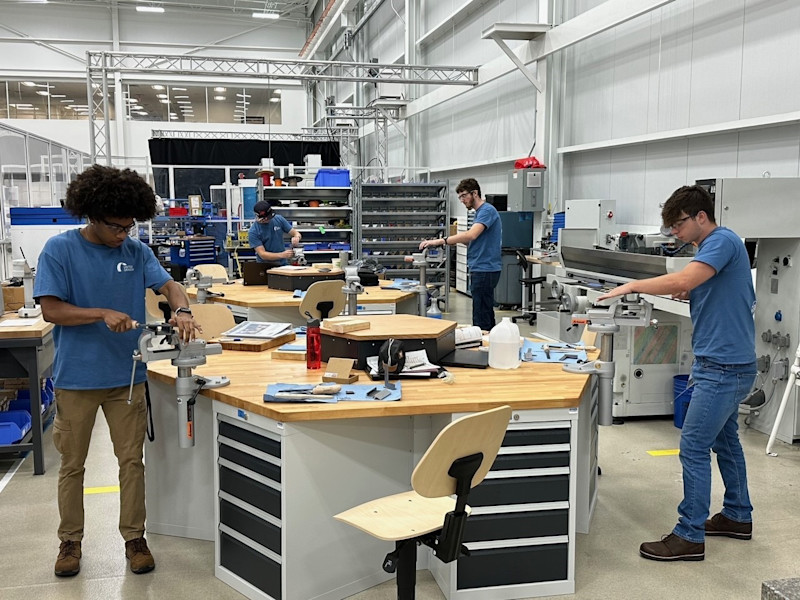
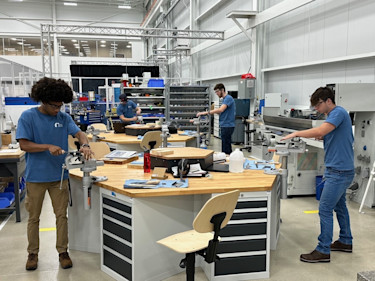
Schunk’s apprenticeship program at its Morrisville, North Carolina, U.S. headquarters was also started by a German apprentice who came to the U.S. and fell in love with the country. The company’s first apprentice graduated eight years ago and remains there, as do six others who have gone through the program. The latest three graduates are working with automation solutions, including collaborative robots and as manufacturing technicians.
As with United Grinding, Schunk offers four-year apprenticeships that lead to an associate degree, in this case from Wake Tech. To further leverage the power of collaboration, Schunk is one of 11 companies involved with “NC TAP,” or North Carolina Triangle Apprenticeship Program,” which works with three area technical colleges.
“NC TAP helps the collaborating companies get college classes scheduled, plus we can guarantee the schools a certain number of apprenticeship seats available,” says Phil Leighton, apprenticeship program leader at Schunk. Currently, Wake Tech has 76 apprentices between the 11 NC TAP companies, including 12 from Schunk.
Training pathway
Okuma also collaborates with a technical college as part of its apprenticeship program, which the company started in 1995 to provide a technical training pathway for service technicians in its distributor network.
Reflecting distributor requests for more skilled workers, Okuma now has 38 apprentices in its program.
Reflecting distributor requests for more skilled workers, the program now has 38 apprentices in its program, up from eight in previous years. To accommodate the increase, Okuma starts new apprentices with a virtual learning component that covers about three dozen courses with Tooling U-SME (the workforce development division of SME).
After mastering these basics, the apprentices move on to the “core” curriculum, attend mechanical maintenance, electrical maintenance, and programming and operation courses through the Okuma Machine Tool Academy (OMTA). OMTA was developed in partnership with Rowan-Cabarrus Community College at its Advanced Technology Center in Kannapolis, North Carolina. Finally, apprentices tackle the CARE curriculum where they attend rebuild, recovery and in-depth troubleshooting courses with the Okuma Constantly Available Resource Experts (which are principal engineers and other subject matter experts).
“Just because you go through an apprenticeship program doesn’t mean that learning stops,” adds Natalie Rogers, CMTSE*, Okuma training program manager. “We have different tiers of technicians. After apprentice, you can become an Okuma certified technician and then an Okuma master-certified service technician, which is a greatness they aspire toward. It opens up more opportunities, including becoming a mentor within the distributorship.”
Reasons for collaboration
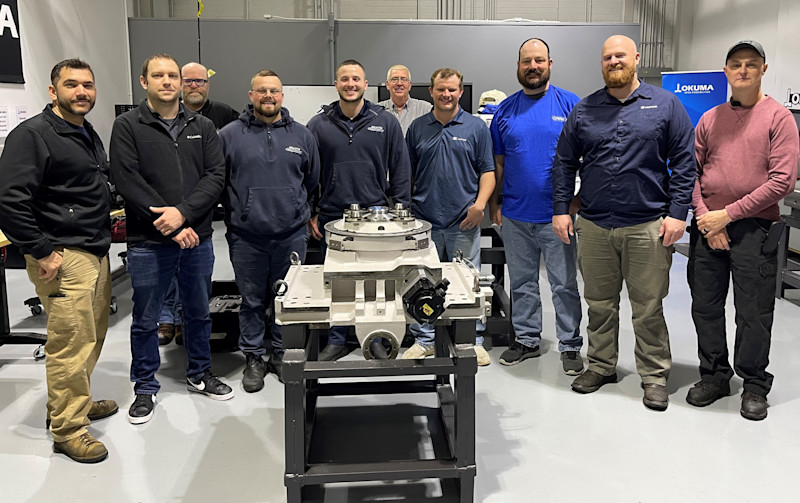
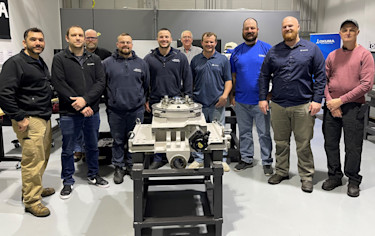
Working with third-party sources serves several purposes. First, it provides apprentices with a strong foundation delivered by institutions who do what they do best: teach the basics. That could include courses in robotics, PLCs, pneumatics, hydraulics, motors, drives, controls, and other courses commonly associated with mechatronics.
United Grinding apprentices attend school two days a week, then spend three days on the job.
Colleges benefit because they cannot afford to make yearly multi-million-dollar equipment investments to stay current with technology. However, by partnering with industry, their apprentices get to train on state-of-the-art equipment and mentor under engineers and technicians who are on the leading edge of innovation.
Leighton, who previously worked as a machinist, says, “I’ve been to the school of hard knocks. An apprenticeship structure provides students not just with knowledge and skills, but with manufacturing-floor experience. When they graduate, they stand apart from those traditional two- or four-year degrees.”
Brockmann delivers the bottom line on apprenticeships for the manufacturing industry. “If you do not invest in the future of your people, will you have a future? Multi-million-dollar machines won’t be solving your manufacturing challenges if you do not invest in people to run them,” he says.
To explore the full breadth of careers in manufacturing technology, secondary and post-secondar students can attend IMTS 2024 and connect with more than 1,500 exhibiting companies. Because exhibitors bring personnel representing the entire scope of their capabilities, people interested in manufacturing careers can connect with service technicians, engineers and others that will share their experiences. Remember: Manufacturers want to find good people for their team!
The Smartforce Student Summit at IMTS 2024 is an area of the show dedicated to students of all ages. Some of the biggest names in manufacturing set up interactive experiences and competitions to introduce students to CNCs, robotics, automation, virtual reality, software, metrology, and much more. Several colleges also exhibit, and their booths staffed by students who are there to connect with the next generation of the manufacturing workforce.
Register at IMTS.com/Register.