2023: the year I had the privilege and pleasure of hunting for manufacturing technology at a handful of end-use trade shows to see how it has been applied in industries that support consumer interests, both niche and popular. The year started with a bang at the SHOT Show, as I recapped in this column in the March/April issue, and ended strong, returning home to manufacturing – though nowhere near home.
SEMA Show 2023
I’ve wanted to attend SEMA in Las Vegas, Nevada, for almost as long as I’ve been into cars. If you’re a fellow gearhead, you know SEMA, the Specialty Equipment Market Association, is not just another global car show for auto brands to show off their latest concepts and current releases. There’s some of that, but mostly it highlights the automotive aftermarket. It not only assures attendees that anything’s possible, but it introduces them to the people, tools, and technologies that can enable automotive personalization.
And that’s why I was at SEMA – prowling for some hot manufacturing technology. I wasn’t disappointed. In fact, I was elated with the tech I found! There was a surprising number of robots – mostly for welding, but in at least two cases, AI-enabled robots were used for paint polishing. While there wasn’t much focus on additive technology, except for the sneak peek at Toyota and Stratasys’ collaborative effort to produce factory-supported race car parts, there was a solid amount of subtractive and CNC machining. In fact, I think SEMA may have marked the first time I’ve ever seen a vertical lathe.
Titans of CNC was there exhibiting a one-piece milled grille/front-end for a hot rod. Someone with no passion might say, “Looks like they made a $50,000 solution for a $500 problem,” but I say they were showing off what can be done when you have full creative and technological freedom and can spare no expense!
For more SEMA breakdowns, follow the AMT Tech Trends podcast. And I want to leave you with this: SEMA is a magical event that, for one week out of the year, turns full-grown adults into 12-year-olds again. My face is still sore from smiling for 120 hours straight.
The Green Hell: Nurburgring Nordschleife
In 1997, Polyphony Digital, a game studio owned by Sony, released a little game called Gran Turismo. An addicting racing simulator, Gran Turismo allowed players to customize everyday cars (and supercars) and adjust settings like ride height, damper stiffness, and gearing before competing on digital racetracks based on real ones from around the world. It sounds like a digital twin to me! The “game” series, which would go on to sell over 90 million copies, was recognized by the FIA and could even greatly assist you in obtaining your international racing license. Even better, if you ranked among the best online players in the world, Polyphony Digital and Nissan invited you to join their GT Academy, where you’d be trained on a real race car and be given the chance to jumpstart an international racing career. Yes, they made a movie about it.
But let’s throw it in reverse for a second. In 2004, Polyphony Digital released Gran Turismo 4, the first game in the series that introduced 15-year-old me to the terrifying and legendary Nordschleife (North Loop) at the Nurburgring, a German race track that’s 12.9 miles of high speed, tight corners, and a tighter track width. I only ever tortured myself with this track if the game required it or if I wanted to test a car’s top speed. It’s no wonder it’s appropriately nicknamed the “Green Hell.”
OK, so what? The week after SEMA in Las Vegas was Formnext in Frankfurt – and thanks to having the best job in the world, I got to go! But after almost two decades of putting down digital hot (and not-so-hot) laps, wrecking, and reaching higher and higher top speeds, I figured it was time to see the Green Hell with my own eyes. I’ve driven cars in real life that were developed, shaken down, and proven on the fabled circuit; it was time to observe the physical twin for myself.
Tragically, I wasn’t able to feed my need for speed then. By the time I arrived, the sun was already hurrying toward its dinner date with the horizon. Still, I got to poke around the paddock, smelled the lingering exhaust fumes, and felt the asphalt beneath my feet, where countless generations of sports cars and grocery-getters had battled. It may not have been the rush I was looking for, but the payoff was as glorious and vivid as any my inner 15-year-old could imagine. I had finally set foot on holy land. And for anybody who hasn’t been: It’s real! You may judge me for being corny and cheesy, but I was in tears.
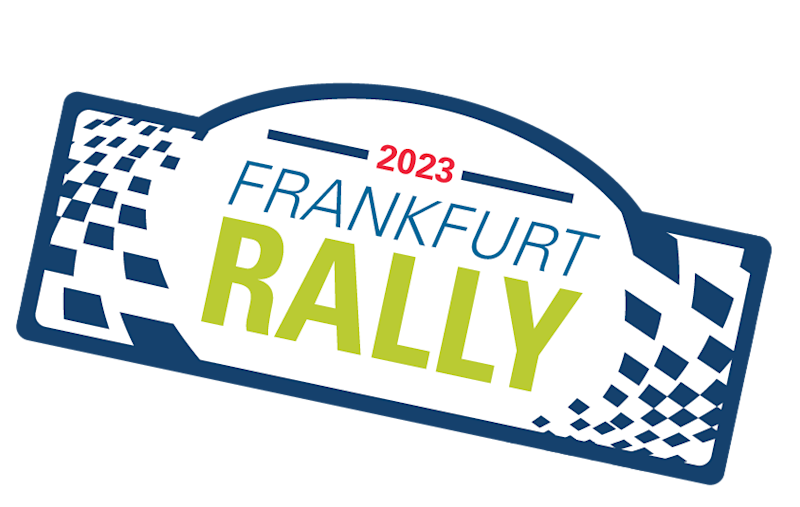
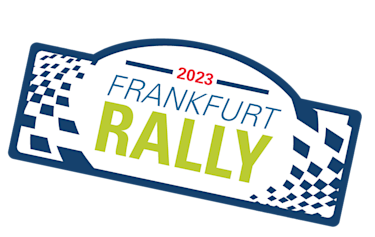
Formnext 2023
Even though I missed my chance to drive the Nurburgring Nordschleife, there was a prize that more than compensated for my FOMO: Formnext. After having spent less than 24 hours at home to swap dirty Vegas laundry for clean clothes and to see family, I arrived in Frankfurt the Monday before the event. As soon as I grabbed my bags, I rented a righteous little Toyota Aygo X, hit the autobahn at over 160 kph, dropped my bags and two of my colleagues off at our hotel, and was green-flagged to the Ring and back. With that pitstop out of the way, it was time for work.
Formnext was awesome! No wonder we’re partnering with Mesago. There were more cars there, notably three modern F1 cars (but not from the current F1 season). More importantly, I finally saw manufacturing coming to additive – or vice versa, additive coming to manufacturing.
I know I’ve said it a million times, but I’ll say it a million more: Additive manufacturing is no longer an emerging technology; it has emerged. Now, if we in the manufacturing industry want to see additive manufacturing become successful, we need to see AM integrated fully into the rest of the actual production (aka money-making) side of the manufacturing industry. I saw this at Formnext.
Right off the cuff, two traditional manufacturing companies made a huge impression on me – Makino and Grob. Both are very well established. Grob showed off their new liquid metal 3D printer, and Makino showed off their additive integrated manufacturing cell rather than a standalone machine.
Sandvik and Kennametal were also present, two names that are also very familiar with the manufacturing industry. The two companies showcased new tooling solutions, including one created with metal AM for additive users: a lightweight toolholder whose dead space allowed for through-tool cooling.
The last thing I’ll mention about Formnext is my favorite part (which I first saw at IMTS 2022): Elementum 3D’s 3D printed brake rotor. This experimental part came off a Dodge Hellcat test mule, and the entire thing – not just the hat, but the friction surface also – is made of aluminum. A fancy aluminum, but still. I cannot stress the material enough: If a 3D printed brake rotor with lattice cooling vanes can handle stopping a pig like a Hellcat and is made from aluminum, everything I know about materials is null and void.
Elementum 3D’s racing applications are why a certain powerhouse of a racing team has been disgustingly dominant in a certain high-level international motorsport. I was asked to not say more than that.
The point I’m trying to convey is that until this particular application of metal AM and DFAM, making a brake rotor out of aluminum was inconceivable! The audacity – the confidence in their research! Somebody must have said, “Uh, you know aluminum melts easily, right? And brakes, especially racing brakes, get really hot, right? Like white hot. If the rotor melts away, you have no brakes at 200-plus mph.” And they did it! That’s how certain they were about the cooling potential of the internal lattice – which could only be achieved via metal AM. I need to go lay down.
Results and Standings
In the whirlwind journey from the bustling halls of SEMA in Las Vegas, to the iconic Nurburgring Nordschleife, to finally landing at Formnext in Frankfurt, my Q4 2023 manufacturing odyssey has been nothing short of exhilarating. SEMA, with its automotive wonders and technological marvels, showcased the boundless creativity enabled by manufacturing, leaving me awestruck and grinning like a 12-year-old. My pilgrimage to the Nurburgring’s Green Hell fulfilled a virtual dream, and witnessing its majesty in person brought tears to my eyes.
Formnext in Frankfurt marked the pivotal moment when additive manufacturing seamlessly integrated into the broader manufacturing landscape. The entrance of traditional giants into the additive space exemplifies the industry’s evolution. As my journey comes to a close, the resonance of these experiences echoes loudly: Manufacturing is not just an industry; it’s a dynamic force shaping my future, pushing my boundaries, and redefining what was once inconceivable.
To read the rest of the Digital Manufacturing Issue of MT Magazine, click here.