New advancements in machine cutting decrease the need for labor, lower operating costs, increase productivity, and open the door to new markets.
Wire costs cut by a third through innovation
Global EDM machine manufacturer Sodick (IMTS booth 338640) is introducing an innovative new feature on its ALN and ALP wire EDM machine series called iGroove technology. The patented technology rotates the wire during the skim cut operation so that workpieces are machined from top to bottom with all surfaces of the wire.
“One of the key operating costs of an EDM wire machine is the wire itself,” says Dave Lynch, national sales manager, Sodick. “By rotating the wire, we can now use all of it, which reduces operating costs of the machine. In most applications to date, we now see about a 30% reduction in wire usage.”
Previously, only one side of the wire was used, and unlike a saw blade, which can be reused, the wire in an EDM machine passes through the work piece being cut, and then it's collected and disposed of.
Additional benefits of the new iGroove process are better surface quality and greater geometric accuracy on the workpieces themselves. “This is really significant because in the past any attempt to reduce wire usage to save costs always sacrificed those two things, but our new process does not,” Lynch says.
The iGroove feature is unique to Sodick and is standard for its ALN and ALP lines of Wire EDM machines.
Used primarily for stamping dies, molds, and part making, EDM machines are used widely in a variety of industries including medical, aerospace, and automotive, among others.
“As specialists in wire EDM, we have used Sodick EDM machines for more than 20 years and have always been very happy with the services and support the company provides to keep us up and running,” says John Elders, owner, Profile Tool.
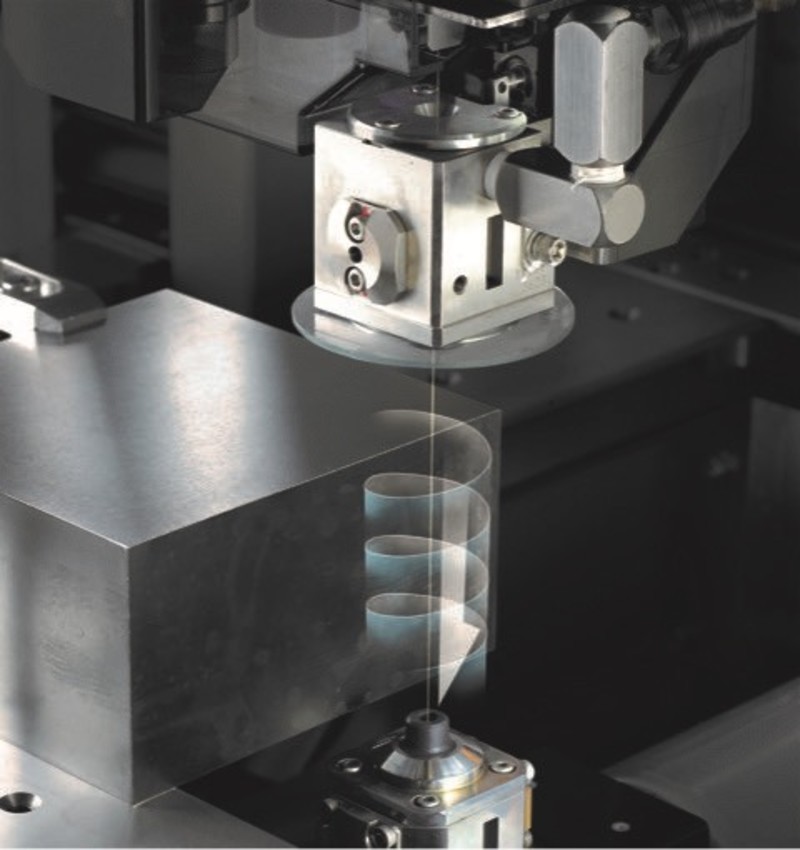
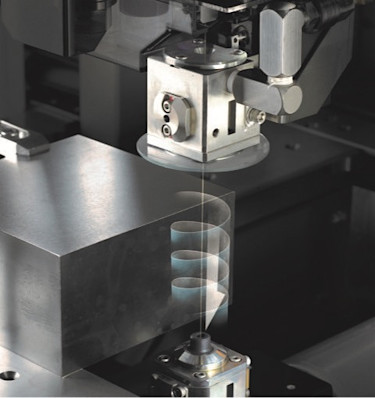
New IFLiPP System speeds turning machine
All manufacturers want to increase productivity, and global machine tool manufacturer Murata Machinery USA (IMTS booth 338844) has recently added a new feature to its twin-spindle turning machine to do just that. The Muratec MW35 machine now sports an innovative new IFLiPP System that allows the operator to quickly load batches of raw fastener materials and keep multiple machines running with short cycle times. The new loading system is faster and more robust with a simpler design and operation.
“With the MW 35, a single operator can easily run multiple machines,” says Jeff Kalmbach, general manager, machine tool division, Murata Machinery USA. “Additionally, the loading system is easy to change over and provides the flexibility needed to run varying part lengths and diameters, which directly translates to increased production efficiency and greater cost effectiveness.”
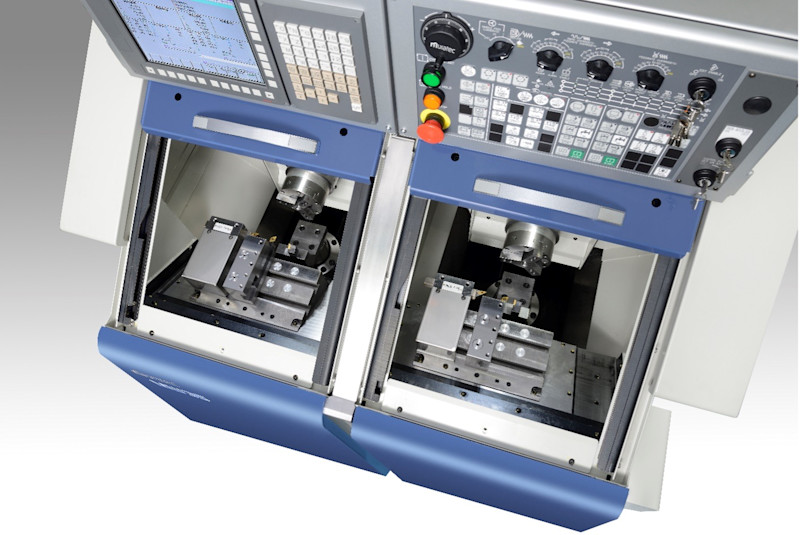
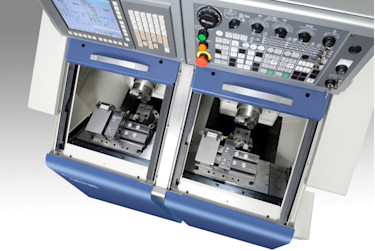
Additionally, its twin spindles enable the MW35 to perform simultaneous operations from a single, self-contained source, making it ideal for manufactured parts that require secondary operations because each spindle can manufacture different processing configurations.
Murata is targeting the automotive and aerospace sectors with this newly added loader feature to help them shift quickly from short-, mid- and high-volume production runs of varying types of fasteners and fittings. The aerospace market is especially ripe for the MW35 since many manufacturers still rely on outdated machine technologies for this type of production. One MW35 can replace multiple antiquated machines in a much smaller footprint, saving both shop space and long-term operating costs. The MW35 allows for much easier setups and changeovers from part to part as compared to the older machine technologies.
C.R. Onsrud to debut new 2022 CH-Series at IMTS
C.R. Onsrud (IMTS booth 338231) will continue its expansion into metal markets with the debut of its new 2022 CH-Series large-format five-axis milling center with new flood and through-tool coolant options. The CH-Series comes standard with a 7’x12’ work envelope and 52” Z-stroke and has been widely used in the large-format aluminum and composites machining industries.
Until now, the CH-Series has only been available with MQL (Minimum Quantity Lubrication) – holding it back from being able to machine heavy metals with maximum chip removal rates. The new 2022 CH-Series has a completely redesigned frame and construction to accommodate flood and through-spindle coolant.
“Adding these coolant options allows the machine to increase speed and allows us to offer higher horsepower spindles, and in turn, our customers can machine tougher and more abrasive materials,” says Ken Stissel, national sales manager, C.R. Onsrud. “We are now able to expand our market to include titanium, steel, and other ferrous materials.
As a result of the new coolant system, C.R. Onsrud has also added a 75-horsepower spindle option to the CH-Series for those looking to machine molds, aerospace parts, and other large-format metal parts. Designed for the global market, companies in the aerospace, automotive, and defense sectors who rely on the five-axis CH-series will benefit from these machine upgrades.
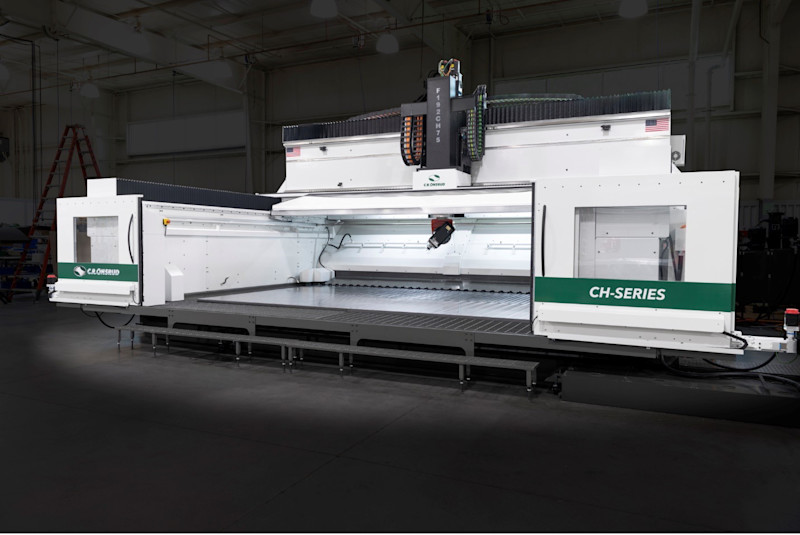
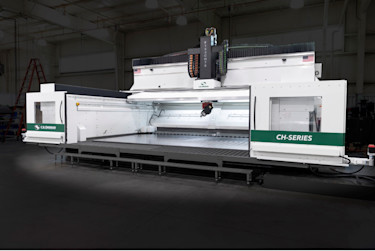
“Our aerospace customers are typically machining structural components made from heavy aluminum such as wing spars. Now they as well as our customers in other markets can machine increasingly abrasive composites,” says Stissel.
Register now and see more metal cutting innovations at IMTS 2022, Sept. 12-17, at McCormick Place, Chicago, Ill. Explore nearly 150 companies in the Metal Removal Pavilion and more than 1,000 other companies exhibiting throughout the event’s eight other pavilions.